Dishwashers, refrigerators, and ovens help determine the look and feel of a home, which is why GE Appliances, a Haier company, believes in eliminating the distance between its business and the customers they serve. Key to their customer-centric approach is their dedication to creating possibilities for employee growth—when employees learn new skills, customers reap the benefits. Read how GE Appliances uses PTC University’s LEARN Online Subscription to help their manufacturing engineers gain Creo CAD software skills and create the premium products that delight customers every day.
GE Appliances believes in finding a better way and creating products for real life
GE Appliances creates world-class kitchen appliances like refrigerators, ranges, and dishwashers, and smaller appliances like coffee makers and toasters. With attention to what customers do and don’t want, they develop features and designs based on the needs of their users.
Established in 1907, today they are an internationally recognized brand with over 15,000 U.S. employees—and their secret is staying committed to employee growth. GE Appliances is a company where employees come together to invent, design, make, deliver and service good things, for life. At GE Appliances, people are celebrated for who they are and the passion they bring to work every day. Despite being a large company, they remain dedicated to the communities where their employees live and work, and they know that investing in people is the best strategy for making world-class appliances for years to come.
New product introductions present process challenges
Key to creating customer-centric appliances is the ability to design and manufacture innovative, new products that meet customer needs. However, the new product introduction (NPI) process involves multiple engineering teams with differing roles and capabilities, leading to inefficiencies.
Each product line at GE Appliances has a dedicated group of design engineers who interface with the Advanced Manufacturing Engineering NPI Group when new products are being developed. The NPI advanced manufacturing engineers create the tools that are then used to manufacture these new products.
GE Appliances leverages the PTC portfolio for a multitude of solutions. When a design engineer requests a new part in Creo, the manufacturing engineer runs a simulation in a separate software to determine if and how the new part can be created.
If a simulation fails, the manufacturing engineer then sends a drawing and description back to the design engineer with suggested changes. There could be a 12 to 36-hour delay between when the design engineer receives notice of the simulation failure and when the manufacturing engineer receives a new version of the part with the implemented changes. This process repeats until a new part passes simulation. Once the part passes simulation, the design team must implement further testing in Creo to approve the fit, the finite element analysis (FEA), and the structural and assembly checks.
Knowing GE Appliances’ commitment to investing in employees, John Panozzo set out to further educate the team
John Panozzo, a senior advanced engineer at GE Appliances in the NPI manufacturing group, knew that if he and his team were to improve their skills in Creo, they would be able to reduce downtime and speed up the NPI process.
One of the main functions of the Advanced Manufacturing Engineering NPI Group is to test the sheet metal formability of a new product, meaning they must ensure that sheet metal can be formed into the desired shape without necking or cracking. Dishwashers, ranges, and washing machines have dynamic and complex surfaces. These exteriors are called Class A surfaces and are frequently at the root of formability issues because they have unique shapes and can include intricate details like tempered glass. Typically, the more attractive these surfaces are, the more complex they are—making them difficult to design and manufacture.
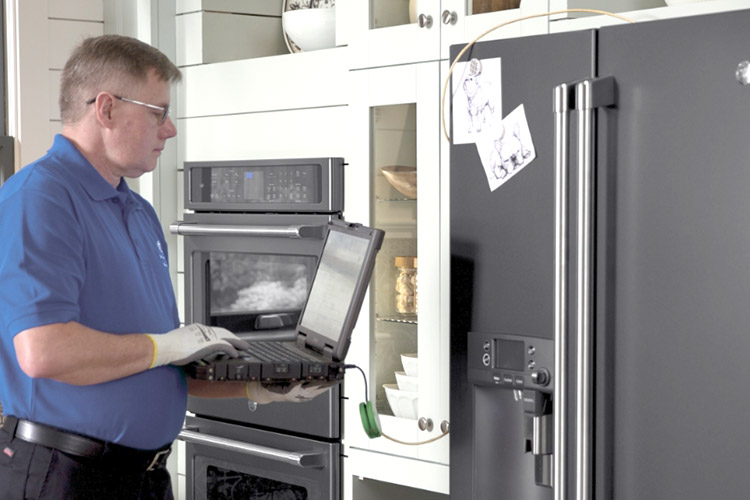
Panozzo knew that if he and his team could increase their ability to work with surfacing in Creo, they would greatly accelerate the process for building tools to manufacture new products by being able to address surfacing formability issues themselves. This would reduce the time delay between simulation failure and when the updated designs are sent back to the manufacturing engineer. The Advanced Manufacturing Engineering NPI Group needed a learning solution that would help them accelerate the creation of tools necessary to manufacturing new products.
Leveraging PTC University’s LEARN Online Subscription to empower employees and increase efficiency
Just as Panozzo began looking for an education solution, Zaid Subhi, a PTC Account Executive, reached out to him about PTC University LEARN Online. LEARN Online is a subscription-based, online platform that offers users a prolific catalogue of courses on how to optimize usage of PTC technology. It includes live, instructor-led trainings as well as on-demand, e-learning opportunities. LEARN Online also offers certification programs that cover both fundamental and advanced professional knowledge and skills for various products.
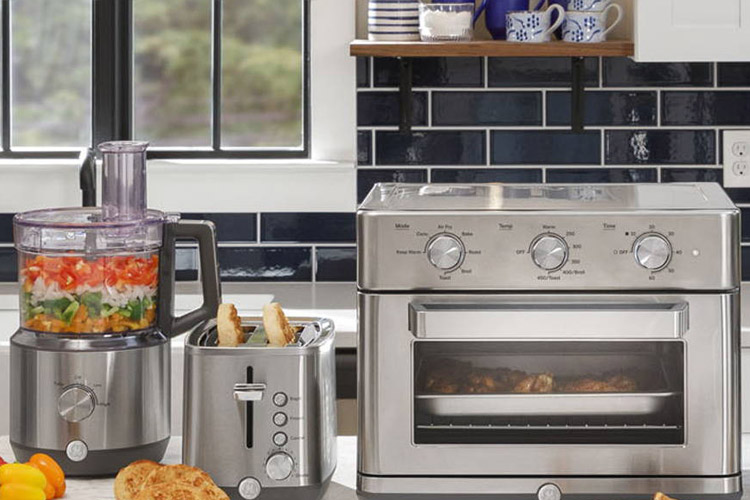
Panozzo recognized that a LEARN Online Subscription could enable him and his team to gain more capabilities in Creo. GE Appliances was extremely supportive of Panozzo expanding his Creo skills, and they purchased a LEARN Online Subscription license to support this journey.
Panozzo was a catalyst within GE Appliances for using LEARN Online to streamline the workflow between manufacturing and design engineers. By attending virtual, half-day, instructor-led courses, Panozzo learned immense amounts of valuable information about Creo that he could implement quickly. “I have learned as much in the nine months of taking LEARN Online classes as I have in my 20 years of using Creo,” says Panozzo. Rather than spend an entire day at a training, these three-hour sessions allowed him to balance his daily duties while providing the long-term benefit of increased productivity and efficiency.
The small, instructor-led courses let Panozzo and other participants interact with the instructor throughout the class, asking questions and receiving answers live. “The instructors do an excellent job of increasing their student’s ability to leverage the powerful capabilities of Creo; they always have time to answer questions either during the session or offline via email,” says Panozzo.
PTC LEARN allows subscribers to re-enroll in classes, which Panozzo found helpful in order to solidify his learning. These live trainings are further supported by the asynchronous e-learning classes that are accessible at any time.
Now, Panozzo reduces the back and forth between his team and the design engineering team because he can implement changes to the surfacing of a new product himself. Through LEARN Online’s half-day classes, Panozzo and his team learned about newer capabilities in Creo to help them address complex surfaces that pose tooling challenges. For example, Creo has the ability to offset geometry, making it easier to work with intersecting surfaces. This is especially crucial when working with Class A and blended surfaces. “Being able to offset to a surface changed my job and changed how I’m able to work with my team,” says Panozzo.
New capabilities in Creo result in 50% time savings
Through the power of PTC University’s LEARN Online Subscription, Panozzo and his team decreased the time it takes to design tools for new product introduction by gaining new Creo abilities. While time savings vary case by case, Panozzo estimates that overall, his group has saved 50% in time.
The NPI engineering group is now empowered to address difficult design challenges, especially as it relates to surfacing, and they have created a culture of learning and advancing Creo skills within their team. Panozzo continues to pass his learnings onto his team to increase efficiency and optimize their use of Creo. In addition, Panozzo encourages interested teammates to take the courses for themselves to up-level their own skills. Several have also enrolled in LEARN Online courses.
– John Panozzo, Senior Advanced Engineer at GE Appliances
As a veteran user of Creo, Panozzo had long been interested in gaining a Creo certification. With the support of GE Appliances, Panozzo was finally able to earn an official Creo certification through the LEARN Online Subscription. Ultimately, this effort supports the greater company culture of employee support and growth at GE Appliances. “I’ve never worked at another company that has invested more in their employees than GE Appliances,” says Panozzo.
PTC University provides best-in-class learning experiences to build in-demand skills and earn industry-recognized credentials. With the PTC LEARN Online Subscription, users can choose a class time that works for their schedule and retake classes as often as need be. World-class instructors lead trainees through a collaborative and engaging learning journey designed to help them retain knowledge and drive success across PTC products including Creo, Windchill, ThingWorx, and ThingWorx Kepware. Learn more at https://www.ptc.com/en/ptc-university.