The design freedom and quality materials provided by HP Jet Fusion 3D Printing Solutions allow Prensilia and Elastico Disegno to create a robotic hand called ‘Mia’
Introduction
Prensilia is an offshoot of Scuola Sant’Anna di Pisa founded in 2009, which manufactures artificial hands and sells them to companies that specialize in prosthetic devices and research.
With academic research backgrounds, members of Prensilia’s team benefit from a combination of academics and business that makes Prensilia one of the few profitable companies in the business of low-volume artificial hands, producing dozens of devices per year with exceptional functionalities and aesthetics. Elastico Disegno is a design and innovation consultancy company established in Torino (Italy) in 1998.
Contracted by Prensilia to bring design and aesthetics to their robotic arms, Elastico Disegno helped Prensilia to fully employ 3D printing to accelerate product development.
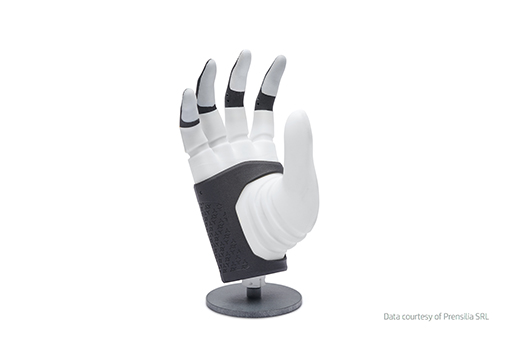
Challenge
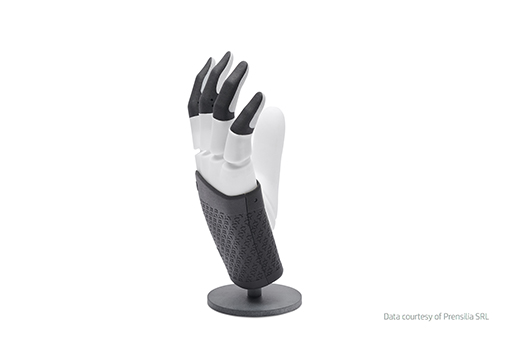
In 2012, Prensilia set a goal to develop a robotic hand that was lightweight, highly functional, aesthetically attractive, and structurally sound in order to protect the device’s internal mechanical and electronic components, with minimal costs for small-series production. Such a challenge would require Elastico Disegno—contracted by Prensilia—to overcome the limitations of traditional production methods and other filament-based 3D printing technologies, such as the inability to perfectly adapt the external covers to the shape of internal mechanics, while maintaining an exceptional surface quality.
The creation of the hand shape and the interior design that must adapt to the internal components required a very sophisticated 3D CAD software, like PTC Creo. Elastico Disegno chose to use PTC Creo as it allowed them
to design mechanical parts and anatomical parts in a single environment, thus accelerating development and minimizing the number of necessary components; flexibly size the product to adapt to any changes in the components; and directly communicate with technical development departments and easily exchange data with the customer to fast-track design iterations.
The project has resulted in anatomical parts that are strong enough to protect and provide structural support for the mechanical parts; complex geometrics that can adapt to Mia’s mechanical components without compromising appearance; fast iterations and fast production; and cost-effective production for limited series.
Solution
Mia features titanium sensors grafted onto a transradial implant between the elbow and the wrist. The cables and electrodes that connect the muscles and nerves pass through the two forearm bones (the ulna and the radius) before reaching the robotic hand, returning the information captured by the fingers and enhancing movement.
The “freestyle” modeling functions available with PTC Creo have enabled an easy design of the anatomical part, ensuring human shape and proportions, and consistency from concept through design to the final product.
Due to the complexity of most of Mia’s parts, Prensilia and Elastico Disegno found additive manufacturing to be the only viable production technology for this project. The transition from the design environment to the prototype or finished product was fluid thanks to PTC Creo’s capability to optimize the components for the print jobs in the same design session and standardize geometry through 3MF files.
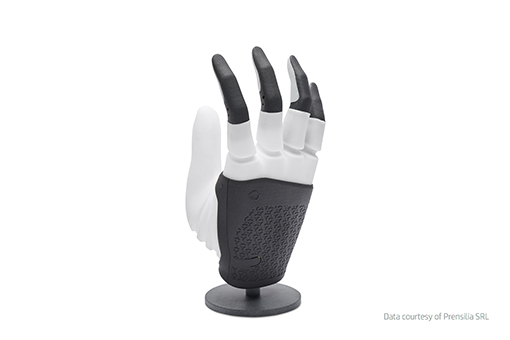
The external covers of the hand and fingers are made using HP Multi Jet Fusion technology with HP 3D HR PA 12 material, which combines strength and structural support as well as a surface finish to ensure the aesthetics desired by Prensilia. These components include parts that are subject to wear, such as buttons and snap fasteners, which passed all functionality tests.
The soft parts of Mia’s fingertips are made from silicone molds, which also are produced by HP Multi Jet Fusion and HP 3D HR PA 12. According to Prensilia, replacing metal molds with plastic molds reduced the investment required and production time, without compromising the performance and surface finish.
In 2019, Mia received the Red Dot Award, an international design award for product design, communication design, and design concepts. Each year, the "Red Dot Award: Product Design" is awarded to the year’s best products with outstanding design quality.
Result
According to Guido Cherici, Partner, Elastico Disegno, "PTC Creo has allowed us to showcase the importance of Italian design, to give it a shape with a stunning product, and to communicate it in the same language of technical developer."
“The first time we tried Mia on a patient, the reaction was, ‘How light!’,” said Marco Controzzi, Founder of Prensilia. “We reached the desired level of robustness thanks to the improvement of the internal mechanics and by 3D printing the external casing with HP Multi Jet Fusion, which allows for the combination of rigidity and surface finish.”
Controzzi also sees the ability to rapidly iterate as a major advantage of HP Multi Jet Fusion technology.
“Another important advantage offered by 3D printing to technological frontier products such as ours is the possibility of offering customers updated products,” Controzzi said.
Mia is undergoing testing in Sweden through the European research project DeTOP (Dexterous Transradial Osseointegrated Prosthesis with neural control and sensory feedback).