AUSA is a leader in vehicle manufacturing
With extensive experience in the market, AUSA is a leading global manufacturer of compact industrial vehicles for material transfer and road maintenance. Learn how they leveraged Windchill to positively redefine cross-departmental communications while improving efficiencies in personnel and processes.
AUSA has been designing, manufacturing, and perfecting its vehicles for more than 60 years. Headquartered in Barcelona, it also has subsidiaries in France, the United Kingdom, Germany, the United States, and China.
They currently have a production capacity of more than 10,000 vehicles per year, 70% of which are exported outside the Iberian market. Its products are present in 90 countries across five continents and are distributed by more than 500 partners.
Communication challenges lead to errors and loss of time
Despite the fact that AUSA had some automation in the transfer of items between its PLM and ERP, their information exchange between systems was highly dependent on Excels and semi-automatic processes. This fact caused errors and wasted time.
Likewise, the PLM software that AUSA had, ModelManager, was very focused on Engineering (Technical Office) correctly managing the Engineering processes, but with difficulties when it came to managing all the processes of creating a new product.
Thus, taking into account these limitations in the processes and tools they used, communication and information transfer outside the engineering department was not efficient, which again caused errors and loss of time.
Consequently, and due to the lack of communication between departments, the engineering lists did not exactly correspond to the manufacturing lists, causing problems in the management of spare parts or in the maintenance of products already sold.
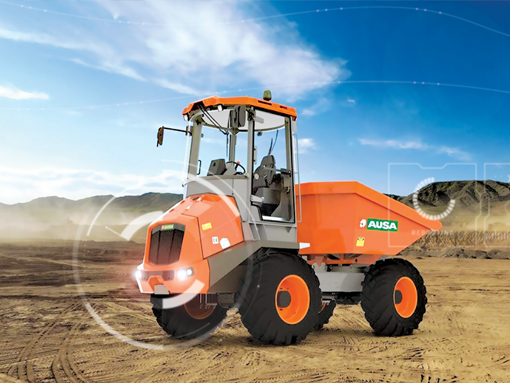
Windchill reduces errors and saves time with automated exchange of information
AUSA wisely decided to implement PTC’s Windchill PLM solution to unify and improve communication between its departments.
Playing a critical role in the success of the deployment, AUSA partnered with Integral Innovation Experts, leveraging their extensive Industry 4.0 experience, consulting expertise, and knowledge of best practices in PLM solutions to ensure successful implementation.
Thanks to PTC Windchill, AUSA managed to have all the technical documentation fully integrated with its ERP, definitely dispensing with the Excels and semi-manual processes that they had to carry out due to the limitations of ModelManager.
By solving this integration problem, AUSA has managed to reduce errors in its work methodology, as well as save time for its workers, by automating the exchange of information between systems.
Likewise, thanks to Windchill’s Access Control, AUSA’s engineering information is currently accessible to the rest of the company, allowing the visualization of both the 3D and the plans to those who have access to those documents, without the need for the intervention of the engineering department.
PTC Windchill has also enabled AUSA to improve collaboration between different departments, thanks to its Change Management functionality, avoiding duplication of files and versions.
Currently, and having solved the problems of lack of communication between the departments, AUSA’s team is fully trained to be able to manage various BOM views. This means that all the engineering lists—manufacturing, spare parts, etc.—are correctly updated and accessible to all those agents that must intervene in the different stages of the process.
Thus, and thanks to the fact that all information is always up-to-date and accessible to all those who require it, AUSA has managed to reduce errors in the manufacture and maintenance of its products.
All the problems that AUSA has been able to solve with PTC Windchill translate into a considerable reduction in errors, which has led to significant savings in time and costs for the company and an improvement in the efficiency of its personnel and
"Thanks to the
integration of PTC
Windchill with our ERP,
we have automated
the exchange of
information between
systems, saving time and
avoiding possible errors
that occurred with the
manual process.”
Albert Hidalgo
R&D Director at AUSA