The OMRON Group conducts business in a wide range of fields, including control equipment, FA systems, electronic components, social systems, and health and medical equipment and services. In 2011, the group has established Value Generation 2020 (VG2020), a long-term 10-year vision spanning up to 2020. “Sense, Think, and Control. For a Brighter Future for People and the Earth.” OMRON’s goal is to become a “value-generator for people and the Earth that is qualitatively and quantitatively superior” to help achieve a sustainable society through their “Sensing & Control + Think” technology. They view the globally intensifying market competition as a growth opportunity and are responding to social needs to solve social issues.
One of OMRON Healthcare’s important missions is to promote “zero events.” Zero events refers to the concept of completely eliminating the onset of cerebral and cardiovascular diseases, such as stroke and myocardial infarction, caused by hypertension. To achieve this mission, OMRON is developing products and services globally by actively engaging with external partners both in and outside of Japan, rather working independently. Thus, by adopting Windchill, information management can be digitalized, thereby increasing the efficiency of product design and licensing acquisition, and creating the time necessary to develop innovative devices. We believe that this will significantly contribute to the realization of their zero event mission.
Digitalization to promote further growth and adapt to the accelerated rate of globalization
In the past, OMRON Healthcare has conducted R&D mainly in Japan, while overseas bases in the United States, Europe, and other Asian countries have designed and sold products to meet local needs. Currently, OMRON is ensuring its capacity to respond to the needs of each country in a timely manner by strengthening its product development system at each of its international bases. OMRON has also acquired the know-how of obtaining permits and licenses in various countries where they operate.
Under these conditions, one of the major challenges faced by their product development departments has been the sharing of digital data. In the past, OMRON’s technical information has been mainly managed by its Japan office. OMRON has also been actively working to digitize its design work and design data by introducing 3D CAD, CAE, PDM, etc. Although the design data had been successfully digitized, the system had not fully utilized the advantages of digital data due to the existence of other data on local hard drives of each representative.
In addition, technical information and audit-related documents were still managed in paper form in thick files, which were kept only at the Japan office. In recent years, OMRON’s businesses have expanded rapidly, with an ever-increasing number of derivative models and frequent changes in design and specifications. OMRON knew that if it continued to use these traditional management methods, it would become increasingly difficult to respond swiftly to such changes. In fact, they have indicated that problems, including delays in updating information, have already been occurring. And they were easily able to predict that problems will continue to grow when releasing products simultaneously around the world, for example.
Responding to audits and ensuring quality were also major issues. OMRON has naturally been implementing measures including QMS (Quality Management System), but as product development processes have become increasingly complex, the limits of conventional methods have become apparent. In addition, one of the most difficult aspects of global expansion is obtaining permits and licenses in various countries. In particular, the requirements for obtaining FDA (US Food and Drug Administration) certification are said to be the most stringent of all regulations in the world. It is always necessary to overcome this FDA certification barrier when selling medical equipment. While FDA applications are being digitized and globalization is accelerating, the existence of a paper-based document management process has been a fetter in the application process in various instances. This created certain problems, such as the inability to find necessary documents and data for the application easily. This also caused inefficiency in the work, which sometimes put pressure on the work hours of onsite technicians.
Mr. Yoshihisa Toki, the General Manager of Development Center, R&D Management Department, Product Development HQ of OMRON Healthcare Inc. describes the situation this way. “Japanese people tend to solve problems with brute force, even if the method is slightly inconvenient. It is true that our conventional system is still working to some degree. However, we were convinced that paper-based information management would not be able to support our processes as our products become more complex and simultaneous global product launches are expected. We believed that we would see quality issues and audit risks if we did not transform the way we manage information.”
At that point, OMRON Healthcare finally began its journey of digitalizing technical documents and implementing PLM. However, to gain the full benefit from PLM, it was critical for the PLM system to be integrated with 3D CAD and other engineering tools, parts management systems, such as the Manufacturing Bill of Materials (MBOM) and Engineering Bill of Materials (EBOM), and enterprise systems including Enterprise Resource Planning (ERP), with a diverse set of systems and data linked to R&D and engineering. In addition, the new PLM system needed to be integrated with the ERP system and data that OMRON, its parent company, manages.
“Integrating multiple systems with very different historical backgrounds and mechanisms, and centrally managing all the data stored in such systems is never an easy task. Digitalizing paper documents prior to the integration work was very challenging, particularly the ones related to audits,” says Mr. Wataru Date, Senior Engineer and Deputy Group Leader of Development Center, R&D Management Department of the Product Development HQ.
Some people in the company raised concerns about whether they would reap any benefit considering all the cost and effort involved, and why they should change the current paper-based process if it is working. However, the sense of urgency of the OMRON Healthcare senior management was so strong that they decided to take a top-down approach to the digitalization initiative and jump-start the project.
This journey will not be an easy one, but this is a mountain they needed to climb and conquer in order to make great strides in their business. The tool they selected for their journey should not be one that would stand in their way.
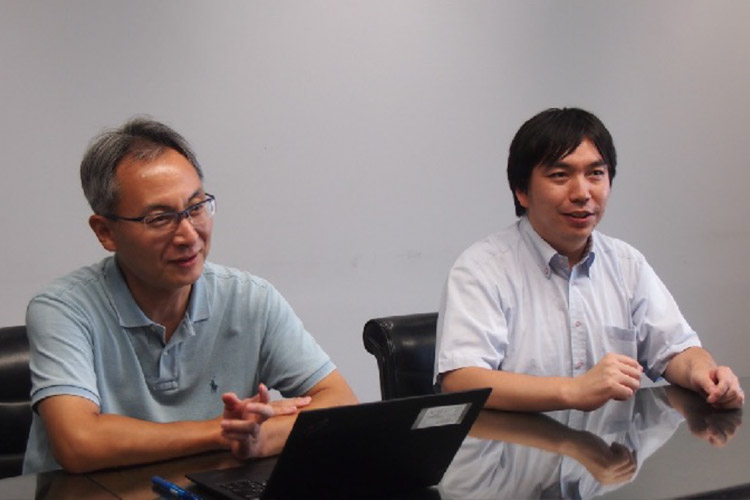
Mr. Yoshihisa Toki (General Manager of Development Center, R&D Management Department, Product Development HQ of OMRON Healthcare Inc.) (on the left) and Mr. Wataru Date (Senior Engineer and Deputy Group Leader of Development Center, R&D Management Department of the Product Development HQ) (on the right)
FDA requirement support was key to selecting Windchill
After going through a process of evaluating a number of PLM systems, OMRON Healthcare selected PTC’s Windchill. What made them choose Windchill?
Windchill is a PLM that has more than 20 years of history, and numerous companies in and outside of Japan have adopted this solution. Windchill provides templates based on best practices developed by existing users, and new users are able to leverage their knowledge and experience. By selecting and adopting the templates that meet the user’s own requirements, they can deploy a PLM solution with little customization. Windchill is a solution that provides a wide range of OOTB (Out-of-the-Box) capabilities.
In addition, Windchill has a Multi-CAD data management capability that supports various 3D CAD systems, as well as various mechanical and electrical CAD data. Users would appreciate the ability to leverage the 3D CAD and other engineering data created in the past. Also, design engineers can access Windchill menus from within their 3D CAD tool, enabling them to easily retrieve data from the PLM system. Windchill provides tools to integrate major CAD software used by various companies.
The ability to share data through the cloud is a critical part of accessing the same set of data from anywhere in world. OMRON believes that it is also advantageous to run Windchill on Amazon Web Services (AWS), a cloud server that is used by the entire OMRON Group, to guarantee the management of confidential information in the cloud. All the technical information will be consolidated in AWS, which enables everyone to use Windchill and access the same set of data globally.
There is also something worth noting about Windchill. Windchill Medical Package, a specialized package for the medical industry that was adopted by OMRON Healthcare, is equipped with a set of OOTB FDA certification support tools that can be used without customization. Windchill Medical Package provides users with templates based on medical industry best practices. This was a key factor in OMRON Healthcare’s decision to adopt Windchill.
This is an area where other PLM tools would require their customers to customize the tool based on specific customer and industry requirements, resulting in additional time and cost for the implementation.
After they decided to implement Windchill, Mr. Toki interviewed PTC users in and outside of Japan. “It was a great opportunity for us to hear not only the success factors, but also the challenges they faced and horror stories they encountered along the way, which they don’t typically share in public. This opportunity helped us move forward,” says Mr. Toki. PTC is also actively engaged in providing such networking opportunities for users.
Windchill helps engineers innovate in the design workplace and harness that power for future products
In my opinion, gathering data that has been scattered in offices around the world into Windchill is a huge advantage in understanding how others are viewing the data. Furthermore, we will be able to understand what kind of data they need and what kind of feedback we should be sending them," says Mr. Date.
“Windchill will help our design engineers around the world think about the types of data that are being used and how these will be utilized. We expect this will also enhance the quality of our designs,” says Mr. Toki. He also expressed his interest in “transforming the paradigm of the design engineers through the effect of the Windchill system.”
”People had limited access to paper-based information, which I think limited the scope of our engineers’ response and thought processes,” says Mr. Toki. “With Windchill, everyone will be able to search for and find the data he/she needs, enabling the technologists to have a wider point of view. Also, junior engineers, now spending much time trying to gather technical materials they need, will be freed from this hassle. Our junior engineers of the future will then be able to spend more time engineering and working on more creative work, which I believe will enhance the level and quality of our design.”
The current scope of the Windchill implementation project at OMRON Healthcare encompasses all areas of design engineering, but the company is also planning on expanding this to other areas of their business, including manufacturing processes, such as MES, and complaint management processes, such as CAPA (Corrective Action & Preventive Action). They also see other opportunities, such as capturing market needs for future designs.
We hope that the implementation of Windchill will help OMRON Healthcare in promoting their zero event initiative and that a day will finally come when everyone in the world will live healthfully.
OMRON Healthcare’s other initiatives
Among the companies of OMRON Group, OMRON Healthcare Inc. is in charge of the healthcare sector. They develop healthcare devices and services, such as sphygmomanometers, thermometers, nebulizers, low-frequency massage devices, and body weight composition analyzers. In 2018, they developed HeartGuide, a watch-sized wearable blood pressure monitor with medical certification, which they pre-launched in the U.S. In 2019, they began selling this product in Japan and Europe, and it is currently gaining popularity.
OMRON Healthcare has also developed the “OMRON connect” health management app, which manages vital data (of the human body) obtained from their devices with communication functions, including sphygmomanometers, body composition analyzers, activity meters, and women's thermometers. They provide various services that utilize these data.
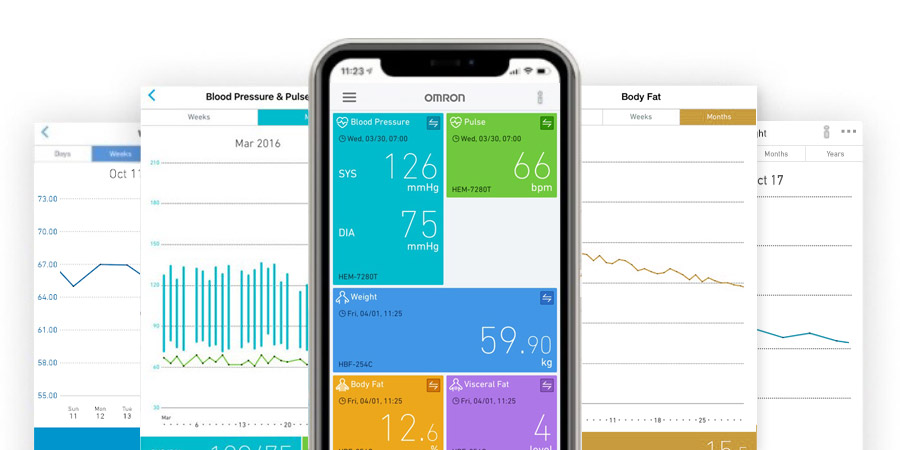
© 2020, PTC Inc. All rights reserved. The information contained herein is for informational purposes only and is subject to change without prior notice. Furthermore, no guarantee, promise, condition, offer or proposal is made by PTC. PTC, the PTC logo, and all other PTC product names and logos are trademarks or registered trademarks of PTC or its subsidiaries, or both, in the United States and other countries. All other product names or company names are trademarks or registered trademarks of their respective owners.