Welbilt delivers customized products that meet specific challenges
Manufacturing has come a long way since Henry Ford famously said, “any customer can have a car painted any color that he wants, so long as it is black.” Now, the mantra for manufacturers who want to remain competitive is the opposite: “any customer can have the product any way that they want.” Success today means being able to efficiently customize high-quality products at scale. Welbilt positioned themselves for success leveraging Windchill in the cloud as the foundation for “mass customization,” embracing product diversity and product lifecycle collaboration to accelerate both time to industrialization and time to market.
Welbilt provides the world’s best chefs, premier chain operators, and growing independent kitchens with industry-leading equipment and solutions. Operating in more than 100 countries with a global network of partners, Welbilt is composed of 12 brands that offer a broad portfolio of full kitchen solutions like fryers, ovens, espresso machines, and more. These brands specialize in delivering customized products and service solutions that fill personalized needs and meet each kitchen’s specific challenges.
Welbilt’s focus on growing market share by addressing their customers’ needs with product variants is most evident in the Frymaster brand. Founded in 1935 and located in Shreveport, Louisiana, Frymaster is a leading manufacturing of fryers and handling and merchandising equipment in the food service industry, supplying food chains and independent restaurants around the world. For almost every product, Frymaster’s customers require deep customizations.
“Each type of fryer has several model families which are highly configurable, meaning the possible SKU counts are in the millions for every product line. Realistically, our assembly lines produce hundreds of possible end items,” says Justin Baker, Engineering Technologist IV at Frymaster.
Frymaster envisioned a unified CAD and PLM system
Despite the high level of customizations required, Frymaster managed their bills of materials (BOMs) with outdated systems and Excel datasets. As a result, Frymaster’s BOMs were disconnected and sometimes inaccurate, creating inefficiencies between engineering and manufacturing teams. This presented a number of challenges, as inaccurate BOMs can lead to increased inventories, reduced economies of scale, service inefficiencies, manufacturing errors, and noncompliance risks. Furthermore, manual and paperbased processes slow down the change notice (CN) workflow, causing a slower time to market and wasted resources.
In order to better manage their data and enable engineering and manufacturing BOM transformation, Frymaster recognized the need to create an effective enterprise system. A unified CAD and product lifecycle management (PLM) system would have several significant impacts throughout their business. First, an improved PLM system speeds the time it takes to implement changes, ultimately reducing time to market for Frymaster’s products. Second, more accurate BOMs reduce rework costs along the assembly lines, increasing first pass yields and time to industrialization. Quality was another key consideration, which Frymaster planned to improve through more accurate and traceable workflows. And finally, a unified CAD and PLM system reduces reliance on paper and manual processes, decreasing the risk of human error and streamlining the entire production process. The opportunity was clear—Frymaster just needed the right partner to make their vision a reality.
PTC Cloud reduces TCO and time to implementation Welbilt and Frymaster are committed to efficiently pursuing new market opportunities while lowering overall lifecycle costs, and PTC Cloud powers their success. PTC Cloud experts helped stand up their PLM solution quickly and securely, with the right configuration and infrastructure. The functionality, performance, and security of the PTC Cloud enables Frymaster to quickly take advantage of cutting-edge technology while reducing TCO and risk—allowing them to instead focus resources on high-value business opportunities.
Frymaster leveraged Windchill in the cloud, supported by PTC VRD
Frymaster has used PTC Pro-E since 1996 and recently upgraded their CAD software to Creo 5, so it was natural for them to turn to PTC for a PLM solution. They decided that Windchill in the cloud, supported by PTC Global Services Value-Ready Deployment (VRD), was the right PLM solution to enable collaboration and drive faster time to value.
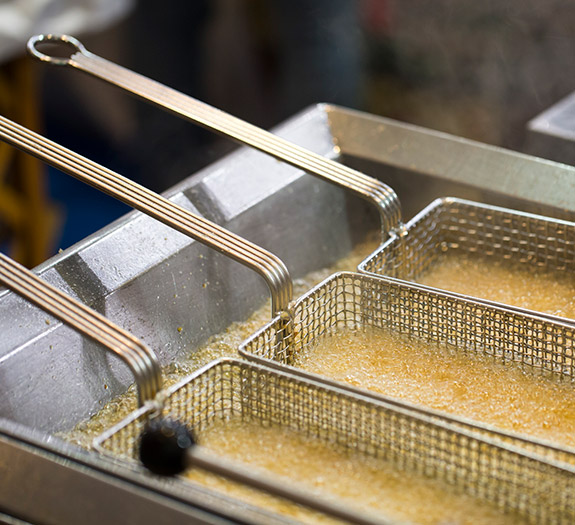
The VRD of Windchill in the cloud is a pre-configured, flexible configuration built upon 25 years of CAD and PLM best practices. The offering includes a selection of enterprise packages and role-based add-ons for engineering, quality, manufacturing, service, and the extended enterprise with ThingWorx Navigate. These SaaS offerings also meet strict security safeguards and compliance requirements. All upgrades and updates are included, as well as dedicated production and non-production environments.
Windchill’s tight integration with Creo and other engineering tools enables a concurrent design environment. When used together, they gain efficiencies in organizing, tracking, and re-using all design data—eliminating tasks that don’t add value and helping Frymaster hit their cost and schedule targets.
“With PTC Cloud, the speed to deployment was a game changer. We were able to complete the first release in four months, and at the same time reduce our TCO and security risks. This is a cloud we can grow with, at a speed that’s right for our business.”
~ Justin Baker, Engineering Technologist IV at Frymaster
VRD on the PTC Cloud reduces TCO and time to
implementation
“Value-ready deployment” means the solution is a proven, ready-to-deploy offering of Windchill in the cloud that can be up and running within months and is fully supported by PTC experts. Frymaster saw value in using PTC’s VRD executed on the PTC Cloud, as it would help them adopt best practices without requiring a full design overhaul. The VRD includes best practices of managing CAD, documents, BOM’s, changes, and configurations. It also includes best practices for integrating with Frymaster’s legacy enterprise resource planning (ERP) to accelerate deployment and adoption. This set up Frymaster to scale the solution to other business units.
PTC Global Services were instrumental in supporting a successful deployment. They conducted educational workshops for employees and helped Frymaster select and customize standard workflows that matched their business model. Furthermore, the entire environment of Windchill in the cloud is maintained by PTC experts, significantly improving the time to value and reducing total cost of ownership (TCO).
“We pride ourselves on delivering agile and scalable solutions. With PTC Cloud, the speed to deployment was a game changer. We were able to complete the first release in four months, and at the same time reduce our TCO and security risks,” says Baker. “This is a cloud we can grow with, at a speed that’s right for our business.”
Frymaster transformed their BOM management process with Windchill in the cloud
Frymaster introduced model-based configuration management through Windchill in the cloud. Now, system models and requirements are connected and accessible to all teams, enabling downstream stakeholders to make more informed decisions. Engineering and design teams can directly access requirements and functions that are critical to part and product design, facilitating the more efficient realization of design deliverables.
In Windchill, 3D models generate a visual BOM that can be easily navigated and interrogated by non-CAD users. New configurations are visually and programmatically evaluated for feasibility. These 3D models replace the need for 2D drawings, which are difficult to interpret by the untrained, prone to errors, and not always up to date.
"Having a PLM that’s cloud-based has enabled collaboration within Welbilt even if they’re not in the same building as us. Employees could even access live updates from across the entire design team"
~ Justin Baker, Engineering Technologist IV at Frymaster
Visual BOMs in the PLM system are then transformed into manufacturing bills of materials (MBOMs). By maintaining a digital connection from the design model to the engineering BOM and downstream manufacturing BOMs, Frymaster provides end-to-end traceability and ensures that any upstream changes are recognized and propagated to manufacturing. For example, Frymaster uses 3D visualizations based on models during the allocation process. This thread is further leveraged in process plan development, keeping it current with any upstream design changes.
On the assembly floor, employees use ThingWorx Navigate in Windchill to look at each unique end item. “Previously, we would build BOMS at the sub-assembly level. Engineering would assist the assembly line and guide them as to how systems went together,” says Baker. “Now, the assembly line teams don’t have to rely on someone else for guidance. It’s a visual reference for where every single component goes.”
Frymaster also use their MBOMs to create a kitting list, so they can equip the manufacturing line with the materials they’ll need that day. “SKU possibilities are so high, and we never really build the same thing twice. It’s really important to have a tool that manufacturing group can use to build kitting carts for the assembly line,” says Baker. Enabling this collaboration between engineering and manufacturing helps Welbilt increase product yields, shorten time to production (and market), and reduce product development costs.
CN workflows have also seen a significant increase in speed. In Windchill, there is a point in the workflow where instructions are sent off in parallel to multiple departments at once. So instead of passing files around, teams can work simultaneously on a single source of truth. By reducing reliance on manual and paper-based processes, Frymaster implements and records design changes throughout the product lifecycle faster and more accurately.
“Windchill has helped us speed up the CN process, and reduce how much paper we waste,” says Baker.
Frymaster fueled increased collaboration and convenience in the time of COVID-19
Soon after they implemented Windchill in the cloud, Frymaster began a new project— but they didn’t have all the resources they needed to complete it in-house. Using Windchill in the cloud, they were able to reach out to other Welbilt brands that use Creo and give them a URL (login and license). Suddenly, they had a greater number of people to collaborate with. Because the software is cloud-based, collaborators didn’t have to be on the same network and could work together from across the country.
“Having a PLM that’s cloud-based has enabled collaboration within Welbilt even if they’re not in the same building as us,” says Baker. “Employees could even access live updates from across the entire design team.”
Working on Windchill in the cloud also made remote work possible during the early stages of COVID. When Frymaster couldn’t return to the office, they were able to achieve the same level of collaboration, security, and productivity at home. Now, they have the flexibility to work however is best for their needs: either at home or in the office (with COVID-related protections).
“COVID hasn’t affected our productivity for design and engineering,” says Baker. “And it’s been extremely convenient. I didn’t have to rely on a VPN connection for my work laptop to access Windchill. If the system was hosted locally, I would’ve had to use a VPN to connect.”
Relying on PTC’s Cloud Services team has given Frymaster peace of mind throughout the process. If there’s hardware or software issues, an employee simply submits a ticket, and the issue is fixed as fast as possible. This is extremely useful because Baker’s department doesn’t have the software and hardware expertise in house to maintain the systems. And the experts they do have are already at capacity.
“If there’s a problem, we submit a ticket and gets resolved in a couple of days. There’s value in that, especially relative to the cost we’re paying,” Baker added.
Frymaster successfully enabled a model-based digital thread
Windchill and PTC Cloud’s capabilities enabled Frymaster to efficiently pursue new market opportunities while lowering overall lifecycle costs. They dramatically reduced time to market by enabling developers to reuse previous designs and speeding time to implement changes. In fact, they experienced a 30% improvement in time to implement engineering change notices and orders (ECN/ECOs). And with a better understanding of work cell or parent location in the system, they’ve decreased the time it takes to build kit lists. Furthermore, they’ve reduced line build rework by 30% through increased BOM and design accuracy. Other significant results include reducing their reliance on paper and manual processes, further improving quality and accuracy.
“If we can have a bill of material that’s 100% accurate and verifiable with a 3D model, the assembly line won’t be negatively affected by that. That means improved quality and time to delivery for the customer,” says Baker.
Welbilt and Frymaster are looking forward to continuing their partnership with PTC
As Frymaster continues to measure the impact of Windchill in the cloud, they expect to realize great results. They are exploring more features and capabilities in Windchill to unlock greater benefits, including implementing supplier management and process planning capabilities throughout their systems. And now that Welbilt and Frymaster have configuration-managed CAD connected to the overloaded BOMs, they are equipped to view specific configurations in 3D and augmented reality. Frymaster expects to use this information to incorporate 3D and augmented reality in their planning and manufacturing process in the future.
“We’re already looking at how we can leverage more tools inside of Windchill, to do the things we’ve done in the past with other systems. This will help us expand and smooth out downstream processes,” says Baker.
Frymaster and Welbilt are in constant pursuit of innovation. With Windchill SaaS on PTC Cloud, supported by VRD, they’ve built a foundation for “mass customization”—enabling them to deliver customized products and improve their own processes faster than ever before.