Eaton Accelerates Industry 4.0 Transformation with a Top-Down Strategy and High-Impact Use Cases that Scale Quickly Across the Enterprise
Achieving Industry 4.0 transformation requires a strong digital foundation
Manufacturers with many factories have two paths to digital transformation. They can either develop and deploy unique applications for each manufacturing facility—which would produce a variety of use cases and inconsistent results—or they can focus on common, high impact use cases that have value across all their manufacturing facilities. With over 200 manufacturing facilities around the globe, Eaton chose to accelerate transformation by leveraging PTC’s Factory Insights as a Service standardized IIoT applications, realizing quick wins, and forming a digital foundation on which they can easily add more use cases.
Harnessing Industry 4.0 (I4.0) technology helps modern manufacturers drive efficiency, increase agility, and outperform their competitors. But the transformation doesn’t happen overnight. Rather, manufacturers need to take stock of current capabilities and lay the foundation—connectivity and a unified IT/OT digital platform—for a wide range of I4.0 use cases. From a strong digital foundation, manufacturers can realize exponential value by developing consistent, repeatable processes that scale across the enterprise and maximize impact.
Eaton is a prime example of a company that implemented scalable, high-impact use cases to transform. Founded in 1911, Eaton is an intelligent power management company with energy-efficient products and services that help their customers effectively manage electrical, hydraulic, and mechanical power more reliably, efficiently, safely, and sustainably. More than 100 years after creating the first gear-driven truck axle, Eaton stays true to their founding principles, maintaining a spirit of innovation that drives industry forward. Today, they employ more than 90,000 people and serve customers in over 175 countries around the world.
Enterprise Governance Council drives I4.0 strategy, goals, and priorities
As the world’s demand for power keeps growing, Eaton answers with products and services that span multiple industries; as a result, they maintain several different business divisions within the enterprise.
Knowing they needed to approach digital transformation with a strategic vision, Eaton established an Enterprise I4.0 Governance Council to foster engagement and establish buy-in from leadership across all divisions. With the goal of increasing efficiency across the enterprise, the council evaluated various challenges and opportunities for growth. By identifying organization-wide goals for improving operational performance, quality, and speed to market, the council brought the top organization-wide priorities front and center. These included:
- Reducing equipment downtime and minimizing human errors to decrease production expenses and improve quality and safety
- Decreasing tooling costs and lead time to reduce overall costs for complex designs
- Shortening changeovers and creating simpler process instructions to reduce training time
- Meeting complex customer requirements and improving delivery timing to increase business, gain customers, and drive revenue
LTI is a global technology consulting and digital solutions company helping clients succeed in a converging world. With operations in 31 countries, they accelerate digital transformation journeys. LTI is a trusted partner to Eaton, providing guidance from their experience and success with other digital transformations in the marketplace. LTI’s expertise with architecture, product selection, solution design, and deployment helped to lay the foundational elements needed to deliver at scale.
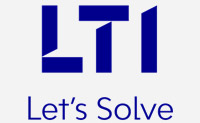
By mapping out their challenges and opportunities for improvement, as well as focusing on deploying consistent applications that could scale across many factories, Eaton began to set the stage for enterprise-wide growth. “We set out to foster a culture of knowledge sharing. Our goal is to make it easier for our employees and customers to solve problems, identify business value, and measure success,” says Craig Sutton, Vice President, Industry 4.0, Eaton. To find the best path forward for every part of their business, Eaton committed to a methodical evaluation process.
Eaton identified high-impact use cases that could scale across all their manufacturing facilities
Instead of letting individual sites develop dozens of unique applications, Eaton knew that scaling standardized use cases across their enterprise was critical to success and high business impact. To identify use cases that could quickly realize value in every manufacturing facility, Eaton began with a year of learning and listening. First, they conducted an inventory of internal challenges, opportunities, and understandings. Next, they studied industry experts, including PTC, and benchmarked against competitors and non-competitors.
“Digital transformation is a journey, but the recipe to avoid pilot and scale purgatory is a top-down commitment for a handful of applications that scale across all sites, followed by rapid bottom-up validation across all teams,” says Sutton.
Eaton selected three key use cases that would scale value quickly across the enterprise and create a foundation for transformation: real-time time production performance monitoring (RTPPM), asset monitoring and utilization (AMU), and connected work cells (CWC). Together, these use cases would have a transformational impact on Eaton, improving overall equipment effectiveness (OEE) and operational efficiency, accelerating product and service innovation, and increasing workforce productivity.
To make their vision a reality, Eaton decided to leverage PTC’s Factory Insights as a Service use cases and the expertise of their Factory Services Unit (FSU). Factory Insights as a Service use cases enable manufacturers to achieve transformational impact with unprecedented speed and scale. Standardized applications for RTPPM, AMU, and CWC—the three use cases that 80% of PTC’s customers start with—are built on PTC’s ThingWorx, an end-to-end industrial Internet of Things (IoT) platform that provides visibility into production and asset health with real-time data analytics, industrial connectivity, and predictive analytics, along with a rich array of insights and reporting.
Leveraging the standard software applications, Eaton dramatically accelerated time to value and created a foundation on which other use case cases can easily be added. “Processes and equipment vary so much from factory to factory. We’re excited to use standard software applications, rather than custom applications,” says Todd Earls, Vice President, IT Digital Design and Manufacturing, Eaton. “With out-of-the-box, standardized offerings, we stay aligned with PTC’s roadmap and receive support from the experts and LTI whenever we need it.”
Delivering flexible tools and scalable applications to improve OEE and enable a digital workforce
Each of the first three use cases is a key part of Eaton’s digital foundation. To start, Eaton is measuring and improving OEE with RTPPM. Relying on real-time insights, they gain a holistic view of their operational performance, helping increase yield and throughput while decreasing cycle times. RTPPM enables a common understanding of manufacturing KPIs, insight into bottlenecks, and data for root cause analysis—essential to continuous improvement. Furthermore, remote monitoring enables touchless operations, which are important from a COVID and social distancing perspective, as they facilitate a safe and accessible source of truth for employees.
Because OEE is affected by machine downtime, AMU is a key companion use case to RTPPM, providing visibility into how equipment performance and health impact overall effectiveness. For example, in an automotive plant in South Bend, Indiana, they are leveraging machine alerts to eliminate the risk of unplanned downtime and detect abnormal conditions within a line of forge units—industrial machines that shape metal through heat and compression. The machine alerts help detect the temperature threshold at which the forge units seize up and fail. The operator then receives the alerts and can correct the issue before production is affected.
“We’re leveraging machine alerts to not only empower operators on the factory floor, but also to provide insight to plant managers and leadership teams, so they can assess and compare performance across multiple plants,” says Earls.
Finally, Eaton is empowering their workforce with the digital tools they need, starting with connected work cells in their aerospace division. With connected work cells, floor operators can access product data and the detailed, digital work instructions necessary to avoid manual errors and ultimately assemble parts in a single, seamless experience. Equipping workers with better tools and data helps decrease errors, increase quality, and enable more flexible processes.
Eaton has successfully rolled out RTPPM and AMU use cases to nine sites. The first three sites went live within nine months, and six more followed in the next three months. They plan on deploying these applications across seventeen more sites by the end of 2021. Already, they’ve realized 10–15% improvements in OEE. Furthermore, AMU has resulted in more than a 12% reduction in unscheduled maintenance.
“In the first four or five months,” says Earls, “We’ve had four different instances where the solutions prevented something from happening which would otherwise cause significant costs.”
While CWC and digital work instructions are still in the early phases of rollout, results are in line with Eaton’s target of an over 15% reduction in manual efforts. Additionally, Eaton has experienced a key objective of 100% adherence to standard operating procedures at that site.
Standard applications that quickly realize value at enterprise scale set the foundation for more advanced use cases
With the progress they’ve made to date, Eaton has laid a flexible foundation for future use cases and capabilities that will unlock exponential value and business impact. For example, Eaton is in the design phase of implementing a traceability use case, ‘track and trace’, across product manufacturing. And by layering in advanced IoT analytics on top of AMU scenarios, Eaton will be able to implement predictive maintenance. “The asset monitoring and utilization framework will help us reach the point of predictive maintenance, and thus prevent a lot of unplanned downtime,” says Earls.
Eaton sees the whole process as more than just going into a manufacturing facility and providing an immediate solution for a specific problem. “Historically, what we would have done was to walk into a plant, deliver a solution like this, and high-five on the way out, having implemented yet another plant application,” says Earls. “We don't want to do that anymore—because the value isn't really the delivery of the solution. It's what you do with it afterwards.”
Billy Ledbetter, Manager, Digital Core Practice, Eaton, agrees that focusing on expanding and scaling capabilities is where they stand to gain the most value. “This methodology allows us to show the problems we solve and demonstrate the results we achieve,” says Ledbetter. “We are not doing technology for technology’s sake, but rather, we have created a consistent, repeatable process to drive value-based outcomes across the enterprise.”
Leveraging momentum and embracing a culture of growth to ensure continued progress
The team at Eaton will continue to leverage support from PTC and LTI on their transformation journey. This year, Eaton has been busy developing skills and building out new learning materials. In particular, they’ve started using Vuforia Chalk and Expert Capture to work with other sites when they can’t send someone in person. They’ve also created a program playbook to document standard operating procedures for new operations.
Perhaps one of the most powerful lessons learned is that a top-down strategy focused on standardized use cases goes a long way when it comes to quickly driving impact at scale. By involving internal stakeholders, Eaton built the support and perspective needed to scale throughout all their manufacturing facilities. And with each use case that builds on their foundation of applications, Eaton is accelerating their ability to tackle things like inventory fulfillment and optimization, augmented-reality-enabled aftermarket services, and connected supply chain management.As Eaton continues to recognize the ways in which a digital foundation allows them to scale—with one functionality opening the door to the next—PTC will continue to empower them with industry-leading technology and support.
“Digital transformation is a journey, but the recipe to avoid pilot and scale purgatory is a top-down commitment for a handful of applications that scale across all sites, followed by rapid bottom-up validation across all teams.”
– Craig Sutton, Vice President, Industry 4.0, Eaton