- Improving OEE
- Digital Workforce Productivity
- Reduce Operational Costs
- Digital Manufacturing Solutions
Evyap has deep roots and a strong commitment to lean principles
Lean processes have long been a foundational concept for reducing waste and improving efficiency in manufacturing. Now the addition of Industry 4.0 technologies is taking value to a whole new level with the potential to reduce scrap and improve production quality by up to 35%.1 Learn how one manufacturer did just that by leveraging IoT technology and the help of a trusted partner.
In manufacturing, keeping up with the competition requires a commitment to continuous improvement and the willingness to examine and refine internal operations—even when that means leading people on a new and unfamiliar journey
One company that succeeded in doing so is Evyap, a Turkish manufacturer of soap and personal care products with a history dating back more than 90 years. Evyap employs more than 3,500 people, transports products to over 100 countries, and operates Turkey’s fifth biggest private port. Despite such busy operations, product quality has remained top of mind throughout its long history, and Evyap remains committed to earning consumers’ trust and loyalty.
Excessive scrap and outdated processes prohibit competitive operations
Back in 2019, the competitive landscape in the personal care industry was significant. Evyap had several competitors, from huge global brands with high-quality products, to smaller local companies that manufactured at low costs.
Across their 50 production lines, Evyap recognized some challenges that prohibited them from being more competitive. First, their lines used equipment that ranged in age from brand new to 30 years old, making for a mixed bag of maintenance and efficiency needs. Additionally, workers from across different factories had very different methods of record keeping, and the lack of consistency made it hard to track progress. On some lines, record keeping was largely paper based, which was slow and inefficient. In fact, they used up to 185 printed forms every day—and within safety and compliance reporting alone, they used 9,000 paper forms per month. This kind of paper consumption was neither efficient nor ecologically sustainable. Complicating matters, longtime management and workers were accustomed to these traditional methods of data keeping and floor operations, and some were resistant to change.
In another area, a particular baby diaper line suffered from problematic stoppages—but the root cause was difficult to identify due to a lack of available, consistent information. Consequently, any scrap, amounting to millions of diapers each year, would end up in landfills since recycling wasn’t an option for these types of materials.
Around that time, the newly formed Operational Excellence Department began to recognize that to remain competitive within the market, the company needed to go lean. Combined with the right technology, Evyap could drive efficiencies within a competitive landscape—but first a culture shift would be necessary.
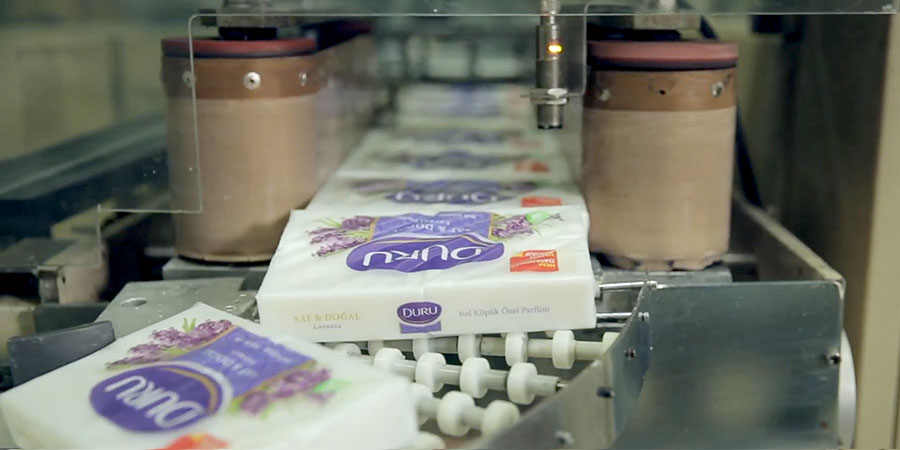
A shift in culture opens the door to a digital transformation
Operational Excellence Manager Emre Erden went to work seeking buy-in from every level of the company, from floor workers up to the CEO. “It was important to convince people at all levels that these new ideas would help them as individuals, as well as the business as a whole,” says Erden. “We believed if everyone in the company supported us through this journey, we could be successful. Without that, we could not.”
Ultimately, what helped Erden’s team achieve buy-in was to identify the quick gains where they could show the most impact in the least amount of time, and then prove they were prepared to select the right technology partner. To do so, Evyap surveyed more than 20 companies in its search for the right team. Recognizing the importance of data analysis, they chose DVM IoT Solutions for its deep expertise in IoT technology.
DVM IoT Solutions is a leader in smart connected operations
A longtime PTC partner, DVM was established in Turkey in 2014 and now focuses on the development of smart applications for businesses of all kinds. As IoT specialists, DVM leverages the ThingWorx Industrial IoT platform to create innovative applications that help customers collect and visualize the data needed to solve pressing business problems. DVM’s partnership with PTC also spans Kepware and Vuforia Augmented Reality technology, as well as past participation in LiveWorx, making them trusted partners in the work to digitally transform businesses on a global scale.
Evyap works with DVM to build a customized IoT solution that drives lean manufacturing
Over the course of four months in late 2019, DVM worked with Evyap to conduct a gap analysis. The results helped determine project objectives and outline a strategy for introducing actionable, real-time information that could help improve production performance, reduce waste, and decrease energy consumption.
By early 2020, the team had perfected an agile process in which they developed, tested, and proved value in the span of just two to four weeks at a time, before repeating the process. This agile approach allowed them to implement a custom tailored, IoT-powered application across Evyap production lines. Built on PTC’s ThingWorx—an end-to-end industrial IoT platform—the new application was first implemented on the baby diaper production line, one of the lines with the highest scrap rates. It worked by leveraging Kepware, a connectivity platform that aggregates machine data and sends it to ThingWorx for real-time analysis. A key benefit of using Kepware and ThingWorx is their flexibility, so the solution could be easily integrated with Evyap’s existing enterprise systems. ThingWorx visualized the real-time production data and provided up-to-the minute predictions and alerts of imminent quality issues and contributing risk factors. This allowed the operators to make real-time adjustments to the parameters that caused faults and resulted in excess scrap. “The IoT data provides key information. The more information we are getting, the more successful we are at solving the problems,” says Erden.
After recognizing immediate value on the diaper line, Evyap and DVM continued to build out the application, resulting in four distinct phases that would scale across other lines and entire facilities. Phase 1 connected the PLCs to the rest of the network so Kepware could collect data and push it to ThingWorx for analysis. Phase 2 leveraged that data and visualized it via dashboards to give Evyap full real-time visibility into the effectiveness of baby diaper and cosmetic production lines. Phase 3 digitized and streamlined all safety management and reporting that was previously done manually. Phase 4 included features to help identify deviations in equipment behavior so Evyap could more efficiently schedule-and in some cases, even prevent—maintenance needs.
The project yielded not only an improved data collection system, but also a way for Evyap to save time and engage its employees in services such as action planning, daily direction setting, and defect handling. “It’s been extremely beneficial to workers because instead of making the engineers analyze the whole dataset, ThingWorx saves us significant time and effort by doing the analysis for us,” explains Erden.
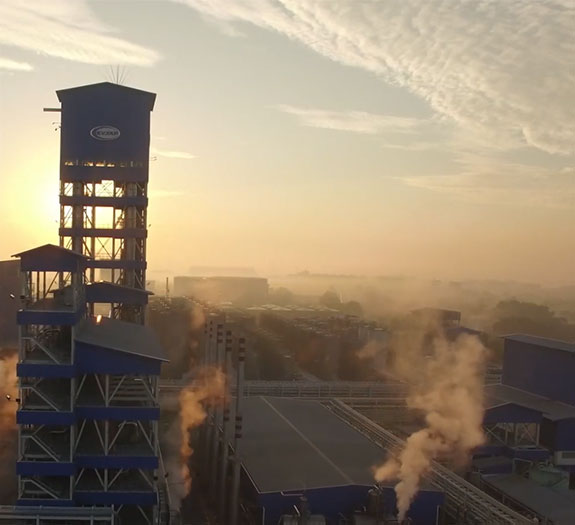
Furthermore, any production, maintenance, quality, or safety defect found by any employee could be entered into the ThingWorx-powered application with clear and detailed problem definition and photos. The same employee could also track the status of any feedback or actions and could become more engaged and efficient, versus using email, spreadsheets, or planner trackers. These improvements were key for closed-loop problem solving with employee buy-in.
Pairing lean principles with digitization: inspiration from a real-world use case
The pairing is far more relatable than the average person might think. Evyap’s Emre Erden explains how the company thinks about organizational health and the benefits of technology as a tool for getting lean:
“We want to be healthy as an organization. You can think about this like human health and weight loss. To lose weight people might play sports, eat clean, and walk 10,000 steps a day. They use smart watches and mobile apps that count steps and calories. They enter personal health data, and the technology analyzes that data and optimizes their exercise routines, resulting in better health outcomes.
“As a company, we’re aiming to lose weight and improve organizational health in a similar way. That means reducing our waste and manufacturing costs—reducing consumption all around. It means working with our people to adopt daily digital, lean practices that improve the health of the company.
“In both cases, digitization is the tool needed to support the main goal. That’s why it was so important to build our lean program principles first, then leverage our work with DVM to begin the real digital transformation. Their IoT solution has been a great tool to support our whole lean journey.”
Evyap reduces scrap while improving OEE and employee engagement
By improving visibility throughout the manufacturing process, Evyap was able to identify critical bottlenecks and inefficiencies. They also reduced waste, maintenance expenses, and indirect costs; improved machine and worker efficiency; and shortened cycle time. Furthermore, they reduced scrap on the diaper line by 23%. This equates to approximately 2 million diapers and a savings of about 2 million Turkish lira, or $250,000, resulting in a positive ROI in less than two years.
Evyap saw improvements across other factories, as well. In one of their aerosol factories they achieved 2% more overall efficiency thanks to improved machine visibility and personnel planning, and they saw a 3% OEE increase in the hygiene factory thanks to improved equipment breakdown tracking.
What’s more, Evyap eliminated five tons of paper and saved 1,500 hours through their form management module that digitalized all paper forms used in the factory. The safety incident rate improved by 60% with the behavior observation system, and after digitizing their data, 98% of products passed quality inspection—up from a previous 75%. Notably, Evyap also achieved one of their most important goals: 100% employee engagement and direct feedback, proving that buy-in from all levels of the workforce matters for achieving success.
The future is bright for Evyap
In the coming weeks, Evyap will go live with newly installed 65” dashboard screens that display ThingWorx data and help all workers assess monthly progress through important KPIs. In the coming months, Evyap is eager to gather and analyze more ThingWorx data so they can roll out a predictive maintenance module later this year. This module will allow them to detect operation faults and possible defects in equipment and fix them before they result in failure. This will help curb additional scrap, especially on the diaper line.
They’re also looking forward to exploring more ways to engage their workforce and revitalize appreciation for new ways of working. “Some people were hesitant at first to take on all these changes,” says Erden. “But now they’re thinking about how this new technology can make their workday better. Now they’re coming to us with ideas instead of challenges,” he continues. “This digital transformation was also a cultural transformation for us.”
"In the last two years, all the engineers we interviewed have said, ‘I applied for this job because I heard about a lot of exciting digitalization projects, and without that, I wouldn’t apply.’ This project created some buzz around our company, and a whole new workforce is recognizing us for our technology."
~ Emre Erden, Operational Excellence Manager, Evyap
It’s not just the current staff that is more engaged. Applicants are noticing what’s happening at Evyap as well, explains Erden. “In the last two years, all the engineers we interviewed have said, ‘I applied for this job because I heard about a lot of exciting digitalization projects, and without that, I wouldn’t apply.’ We are hearing this at all levels,” says Erden. “This project created some buzz around our company, and a whole new workforce is recognizing us for our technology.”
Thanks to its deep partnership with DVM, Evyap looks forward to advancing as a technological leader, putting sustainable operations and consumer satisfaction at the core of its work. “I think we’ve taught each other a lot about our work, and this has really helped both companies,” says Erden of their partnership with DVM. “I think that’s a win-win for everyone.”
1 https://www2.deloitte.com/us/en/insights/focus/industry-4-0/digital-lean-manufacturing.html