From bread to biscuits, think about the precise steps required to bake a delicious treat. Everything needs to be done at the right time, in the right order, with the right ingredients, and at the right temperatures, so you don’t end up with a tasteless lump. Now imagine this process on an industrial scale—the coordination it takes for entire factories and thousands of people to efficiently produce millions of baked goods.
The Griffin’s Food Company is always looking for ways to improve their processes
Headquartered in Auckland, New Zealand, The Griffin’s Food Company is one of the largest packaged foods manufacturers in New Zealand. Over 150 years, they’ve built themselves into an instantly recognizable brand by baking some of New Zealand’s favorite biscuits and snacks. They have two manufacturing sites in South Auckland; the first mainly manufactures biscuits and crackers and the second produces packaged savory snacks, like crisps (i.e. chips) and muesli bars.
Griffin’s takes pride in their business and are always looking for ways to improve their operations. However, like all food manufacturers, they face razor thin margins and steep competition. To keep their position as an industry leader, they constantly look for ways to accelerate production and improve the bottom line while maintaining their high standards of quality. When they wanted to improve the processes behind what they do best—baking delicious food for New Zealanders— they embraced Industry 4.0 technology.
In 2020, Griffin’s had
an initial goal of going
paperless at their
manufacturing sites,
but their vision
quickly grew
Along all of Griffin’s production lines, many operations were performed manually with paper: quality checks, safety checks, recipes, recipe alterations, and reporting. As a packaged food manufacturer, they have to adhere to stringent regulations, requiring them to keep an extensive audit trail.
These paper-based processes slowed down their operations and created opportunities for human error. On occasion, they resulted in missed outages and performance issues that were deemed “too small” to report. Manual reporting delayed performance information and reporting to the point where critical adjustments sometimes couldn’t be made until the next day. Coming up with a digital approach to their paper-based processes was an obvious starting point to Griffin’s Industry 4.0 initiatives.
With the support of Peter Richardson, the Director of Operations and Supply Chain at Griffin’s, the continuous improvement team—led by Vaibhav Tanksale, Head of Capital Investment and Continuous Improvement, Ramy Ragab, Electrical and Automation Projects Manager, and Neil Broekhoven, Process Improvement Manager—are a small team dedicated to embracing Industry 4.0. Beyond going paperless, they quickly recognized an even greater opportunity for digital transformation. They proposed digitizing the production lines by connecting machinery to capture key performance data and displaying it in a unified view. This would open the door for powerful analysis and improvements across their manufacturing sites. The team’s approach was to start small, maintain a clear vision, and scale quickly—ultimately setting themselves up for broader digital transformation.
Tanksale’s team began by establishing a business case. His vision was to equip operators and managers with screens and tablets that displayed previously paper-based information, so that factory workers would have the real-time data they needed to accelerate decision making along the lines. But going one step further, they also planned to show operators and managers any information they might need across all the production lines in real time.
Visibility into production performance opens the door to significant opportunities around throughput, quality, and efficiency. For example, biscuits are difficult to cook. Slight changes in humidity and temperature can cause unnecessary waste. With real-time data regarding the weight, temperature, humidity, and ingredients of their dough, teams can rapidly determine if dough meets quality standards or if it needs to become waste. Operators are able to better understand and improve throughput with increased visibility into asset health, operational efficiency, and unplanned downtime. And with insight into what works and what doesn’t, managers can make faster, more informed decisions around efficiency.
“The first step of this journey is linking the whole factory to the network and getting all our data into one place. PTC gave us easy access to our PLCs and controllers on the factory floor.”
Ramy Ragab
Electrical and Automation Projects Manager
Griffin’s partnered with PTC to implement a flexible IoT solution that fueled connectivity and visibility
After establishing a clear business case, the continuous improvement team set out to find a solution that would turn their vision into reality. The team identified PTC’s ThingWorx Industrial IoT Platform as the right solution for their Industry 4.0 project and they partnered with PTC to begin implementation along their production lines.
Griffin’s chose ThingWorx as their IoT solution for several reasons, the first being its speed of implementation and ease of use. Even with a small team, the solution could be deployed in weeks, rather than months, enabling project leaders to quickly prove value. Even more impressive, Ragab and the continuous improvement team were able to teach themselves all the necessary skills for implementing ThingWorx as they went.
Another key factor was the flexibility and connectivity that ThingWorx enables. Using ThingWorx, Griffin’s could connect the solution to a variety of PLCs and legacy machines in a single, consolidated view. “The first step of this journey is linking the whole factory to the network and getting all our data into one place. PTC gave us easy access to our PLCs and controllers on the factory floor,” says Ragab.
The team started small and demonstrated value quickly
Griffin’s began their digitization effort with a single machine, when Ragab connected ThingWorx Manufacturing Apps to a chocolate mixer’s PLC. As a catalyst for the project, they used Manufacturing Apps’ ability to connect disparate factory machines into a holistic, real-time view of production status and maintenance issues. The team was able to quickly implement a bespoke solution that allowed them to see exactly what the machine was doing, when it was running, the recipe being used, and how much material was being consumed over time. The transition from paper-based reporting to detailed data flowing in real time was dramatic.
The visibility Ragab demonstrated won the backing of operators and leadership. Management supported further expansion of the project to leverage the maximum benefits available. By starting small, proving how monitoring machine performance could help them improve quality, efficiency, and throughput, and establishing a successful implementation process, the team could then quickly scale the initiative to full production lines.
Industry 4.0 is about changing people and culture. Getting the support of both leadership and factory-floor workers is a critical step in that process. When Ragab and the continuous improvement team demonstrated the value of their proof of concept, they set the stage for an important cultural shift, as well as an operational one.
After initial success, Griffin’s began to scale the initiative
In a matter of months, Griffin’s built on the initial Manufacturing Apps initiative and scaled the ThingWorx IoT Platform to three full lines. The remaining four are currently planned for implementation. Ragab then created a central dashboard that gave factory workers, operators, and managers access to production data.
Because the production lines are so long, teams typically don’t have visibility into what’s happening on the other end of the bakery. To mitigate this, the continuous improvement team set up monitors along each production line so that bakery floor workers can see production data in real-time.
Now, workers can see what’s happening upstream and better understand how much time they have to prepare for the new product coming down the line. Ultimately, operational teams are able to use the data to track production performance and throughput.

Using the tablets, operators track all stoppages, including micro-stops, without impacting efficiency. If there is a stop on the line, the employee is automatically prompted to enter the reason for the stoppage. Stoppages need to be categorized as a mechanical issue, quality issue, or product issue. The line can’t be resumed until the information is entered. Line Managers also see a holistic view of where and why the lines are stopping, which enables them to make quick decisions in reaction to stoppages or escalate issues as required.
Quality teams leverage the tablets to track key metrics like weight, temperature, and humidity, enabling them to quickly conduct quality checks for the recipe. If something goes wrong during the quality check, teams can look back and investigate the recipes to see how ingredients were used. By testing and tracking quality continuously, teams save time and materials by designating food as waste sooner and prevent quality issues from reaching customers.
Managers are able to access all of this information on their desktop computers. With greater visibility into throughput, performance, and quality, they can quickly mobilize support for teams or adjust processes to improve efficiency. “We have three screens on the factory floor, and all of the operators are using it. I have four screens that managers can use to see what’s happening. Everyone has responded positively to having greater visibility—they can do their jobs better and more efficiently,” says Ragab.
“You can see operators are moving more dough and chocolate through the lines. We’ve been monitoring them for two to three months and you can see that they’re getting better.”
Ramy Ragab
Electrical and Automation Projects
Manager
Griffin’s successfully set themselves up for future growth and digital transformation
The continuous improvement team’s efforts to embrace Industry 4.0—and thereby improve quality, efficiency, and throughput—were a clear success. They established their business case, quickly proved value to stakeholders, and scaled their IoT use case in a way that made sense for the business.
The time to value was short and the benefits of enhanced visibility are already clear, with indications of increased throughput and efficiency. “It motivates the operators to hit their targets. You can see they’re moving more dough and chocolate through the lines. We’ve been monitoring them for two to three months and you can see that they’re getting better. And they’re getting faster,” says Ragab.
The journey wasn’t always a linear one, and
Griffin’s realized unexpected value along the
way. For example, the initiative has generated
increased communication between departments.
By asking themselves and others how they can
improve performance, teams have increased
productivity and efficiency. “The good thing about
these systems is people start asking themselves
how they can improve,” says Ragab. “People
start to interact with each other, ask each other
questions, and question the live data.”
Griffin’s is already planning to expand their use case beyond production line performance. To help the maintenance team improve uptime, they’re exploring initiatives around monitoring the efficiency of specific machines as well as performance and health across all their assets. Ragab says his team is creating a standardized view for each factory that will display production, quality, maintenance data, and more, giving all users a window into anything they might need to see.
Beyond visibility and performance, Griffin’s also envisions a future where teams have direct control over aspects of production. They want to give operational teams control of the ovens, in order to adjust parameters based on temperature, moisture, and color of the dough. This would eliminate the need to perform adjustments manually and reduce mistakes like burnt dough. And giving product developers insight and control over recipes allows them to track and evaluate ingredient usage for each recipe, as well as alert operators to changes in recipes or new recipes. This way, product developers could improve the quality and consistency of their baked goods and reduce waste.
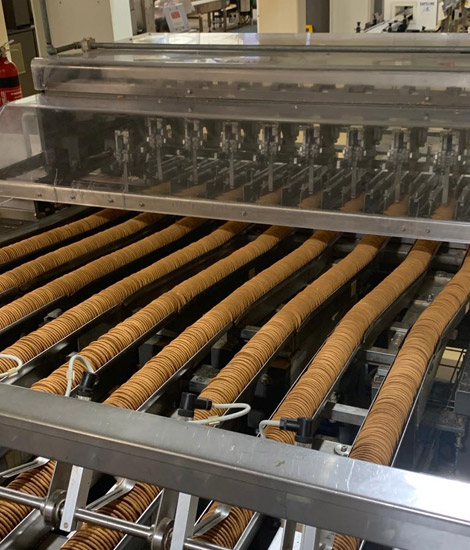
“I see improvement, I see a difference,” says Ragab. “We have more to do, but we are heading in the right direction.”
For Griffin’s, achieving digital transformation didn’t require a leap of faith or significant risk—it required the right strategy. By focusing on impact, speed, and scale, Griffin’s set themselves up for a successful digital transformation journey. With a strong vision, clear business case, and the ability to prove value quickly, digital transformation is within reach for any manufacturer.