- Service Optimization Solutions
- Industrial Connectivity for Machine Builders
- Maximizing Revenue Growth
- PTC Cloud
IMA Group is a leading manufacturer of automated processing and packaging machines
Dedicated to innovation, the IMA Group recognized the potential profits locked in production data. Using ThingWorx, IMA built a customer-facing application that delivers data-driven insights and revolutionized their own service offerings— differentiating themselves from the competition and helping customers drive significant efficiency improvements.
Headquartered in Bologna, Italy, the IMA Group is a global business that delivers machines, services, and solutions to a wide variety of industries, including pharmaceuticals, cosmetics, food, and tea and coffee. They have more than 6,200 employees and 46 manufacturing sites across the globe, and 80 countries within their network. In 2019, their worldwide sales totaled about €1,595.5 million.
IMA has a long history of leveraging new technologies to deliver value to their customers. Building on their legacy of innovation, IMA Digital was founded in 2016 to drive the implementation and adoption of digital opportunities across the IMA ecosystem. IMA Digital’s goal is to understand how new innovations can benefit the company and their customers. They began with 18 digital transformation projects, then quickly expanded to 25. These initiatives span across client services, internal processes, and products, and focus on capabilities like predictive maintenance and remote assistance.
Unlocking the power of data
IMA recognized that by helping customers leverage data-driven insights, they could deliver more valuable solutions and services. First, IMA wanted to give customers the tools to improve efficiency. “There is no way to improve efficiency without better insight into operations. We wanted to give our customers in-depth knowledge of their production processes through the analysis of production data,” says Pier Luigi Vanti, the Information and Communications Technology and Industry 4.0 Corporate Director at IMA.
Second, they wanted to provide expanded service offerings that help customers improve overall equipment effectiveness (OEE) and reduce downtime. IMA offered traditional services (spare parts, technical assistance, etc.) but they wanted to move from product-centric services to more advanced, customer-centric services. This would enable IMA to develop a stronger partnership with customers, differentiate their service offerings, and create new revenue streams.
“The world is moving towards servitization. We wanted to take the relationship with our customers to the next level, which is what has inspired us and guided us on this path of continuous improvement."
Pier Luigi Vanti
Information and Communications Technology and Industry 4.0 Corporate Director at IMA
“The world is moving towards servitization. We wanted to take the relationship with our customers to the next level, which is what has inspired us and guided us on this path of continuous improvement. The real competitive differentiator is no longer around machines, but the level of service we can provide to customers,” says Vanti.
While they had started some of these initiatives before COVID-19, the pandemic only accelerated the need for digitization. Remote collaboration and services became a necessity and an integral part of IMA’s strategic goals. “We accelerated the adoption of these digital transformation initiatives. Increasing remote collaboration was not a matter of efficiency, but of absolute necessity,” says Vanti.
ThingWorx enables data-driven insights and new service offerings
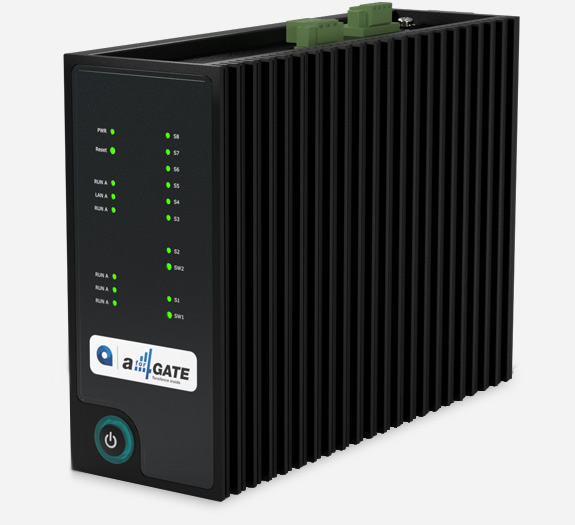
IMA’s integrated hardware and software solution protects data, optimizes system operations, and enhances operator safety.
With a clear vision for a customer-facing solution and improved service offerings—both powered by data-driven insights—IMA decided to work with their trusted partner of 22 years, PTC. Longtime users of PTC’s Creo and Windchill solutions, IMA decided that ThingWorx was the ideal Industrial Internet of Things (IIoT) platform for their initiative. ThingWorx Kepware Server would provide the connectivity.
ThingWorx is a powerful IIoT solution that fuels asset monitoring and automation scenarios by connecting, collecting, and analyzing data across assets. ThingWorx is a reliable and secure solution that enables IMA and their customers to rest assured their data is safe. The solution provides the flexibility that IMA needs, offering a broad set of capabilities and integrations that open the door to leveraging other solutions in the future.
ThingWorx’s rapid time to development and ease of use when deploying features were key considerations for IMA. “We finish one thing, and we already have ten more in mind. As we continue to move forward connecting machines and increasing capabilities, we needed a platform that would allow us to develop and implement new features and use cases quickly,” says Martina Stefanon, Business Development Manager at IMA.
Alongside ThingWorx, ThingWorx Kepware Server was fundamental to facilitating industrial connectivity across new and legacy equipment. Kepware Server provides the flexibility that IMA needs to connect a wide variety of legacy machines and PLCs, built at different times with different technologies. This way, they can easily connect legacy equipment in the field to make older assets “smart.”
Universal connectivity also enables IMA to become a digital solutions provider and capture a larger market share. With Kepware Server, they are ready to connect any type of packaging machine, even if it wasn’t produced by IMA. Additionally, Kepware Server’s industry leading security capabilities provide a unidirectional network from machine PLC to ThingWorx, blocking any external requests or interactions with machine data.
IMA chose to use ThingWorx and Kepware Server on the PTC Cloud, simplifying solution administration and enabling scalability. The PTC Cloud allows IMA to speed time to value and focus resources on high-value business opportunities. Because IMA can connect more assets and grow storage requirements as necessary, ThingWorx in the PTC Cloud provides a seamless path to scale.
Sentinel gives IMA’s customers the tools to better understand production processes and improve efficiency
Using ThingWorx, IMA built the customer-facing Sentinel application. Sentinel monitors machine conditions in real time, collecting raw data and translating it into valuable information. The application is a single monitoring and analysis platform offered as a service to customers, displaying all data and insights in a central dashboard. Operators leverage that information to drive OEE improvements.
Sentinel’s key features include intelligent and dynamic action lists to help operators improve efficiency, machine data statistics for smart line harmonization, and average performance for accurate production planning. Because it dialogues with ERP and MES systems and receives and analyzes data from all PLCs, Sentinel is an open platform that can leverage data from all types of machines, not just IMA equipment. “Our customers are able to connect entire lines, not just IMA machines. That is a huge benefit for them,” says Stefanon.
– Pier Luigi Vanti
Information and Communications Technology and Industry 4.0 Corporate Director at IMA
Sentinel has had a significant impact on IMA’s customers. To start, they gain visibility into operations with a 360-degree view of systems and processes. “Customers report that the system is extremely useful in helping them understand everything that’s happening. Even noticing something trivial can have a huge impact on operations,” says Vanti.
Furthermore, customers are improving efficiency with advanced analytics. “To increase production efficiency, you first need to understand where those inefficiencies come from,” says Stefanon. Sentinel enables customers to do just that, with the ability to conduct real-time analysis into efficiency losses and their source. It even provides smart recommendations directed at operators—algorithms suggest where to focus their attention to increase efficiency in the shortest possible time.
Sentinel also enables customers to reduce downtime with benchmarking analysis. The comparisons between similar machines drive understanding of past performance. Visibility into downtime events and their cause gives operators the insights and awareness needed to reduce future occurrences.
And finally, remote monitoring and analysis capabilities have been invaluable during the pandemic, as restricted travel and access to sites made it difficult to provide in-person support. The ability to access remote support, monitoring, troubleshooting, and insights on phones, tablets, and computers was critical during those challenging times. The benefits don’t stop when the restrictions lift either, as remote features have proven to increase remote collaboration and drive efficiency between teams and stakeholders.
IMA Control Room Services enable manufacturers to improve production processes leveraging IMA’s expertise
IMA Control Room Services are designed to help customers make the most of machine data and enhance their production processes. Supported by IMA’s experienced technicians, customers receive detailed reports, specific alerts, and general support 24 hours a day, 7 days a week. The purpose is to help customers quickly take charge of operational problems, with the aim of improving results.
With Control Room Services, customers can count on proactive, remote assistance. IMA support teams interpret algorithms and data—enriched by ThingWorx—from the machines to proactively intervene if there’s an abnormality. Should anything unusual happen, automatic alarms generated by the system alert the Control Room operators. The Control Room promptly informs customers so that they can intervene immediately. If there’s an issue, IMA technicians simply contact the customer and help them resolve the problem. Furthermore, customers can identify long-term trends and improve production performance with access to insightful reporting.
With Control Room Services, manufacturers can rest assured their processes are being monitored and their production will continue to operate efficiently. This is very useful when the customer has too few personnel to support a lot of machines, or when they don’t have the expertise to interpret data. With ThingWorx and Kepware Server, best-in-class security protects critical assets and data and helps customers meet regulatory requirements.
“Often, anomalies don’t have an immediate effect on machine behavior. But by analyzing data, it’s possible to anticipate future anomalies. This 24-hour service allows our customers to sleep easy knowing that IMA technicians will catch any potential issues,” says Vanti.
The IMA Control Room runs 24/7 to continuously monitor
production and respond to alerts.
IMA successfully evolved their service offerings and are already looking towards the future
The tangible results that IMA’s customers have realized with Sentinel are impressive. For example, they’ve measurably improved overall equipment effectiveness (OEE); up to 16% in a specific success case. “For our customers, even just a percentage increase in OEE from IMA’s support offering can translate to six-zero savings,” says Vanti.
Other benefits include improving manufacturing efficiency with benchmark and loss analysis, optimizing production processes with enhanced people engagement and awareness, and reducing downtime. They’ve also been able to generate extra time savings for personnel. In fact, some customers have been able to reduce the time spent in daily and weekly production meetings by 50% (or half), in addition to giving employees a deeper understanding of production processes. And finally, end-to-end security means that manufacturers can connect equipment without worry.
IMA Sentinel provides a complete mobile platform for automated
system performance monitoring.
Today, IMA has achieved their goal of evolving their service offerings and becoming a partner to customers. They went from traditional productcentric services to advanced customer-centric services, and new service offerings enable them to generate new revenue streams. “Trust is something that has always characterized the relationship we have with our customers, and we’ve been able to build on that by giving them better services and advanced tools,” says Stefanon.
They’ve realized unexpected benefits as well. “The interesting thing is the business model had positive repercussions on our entire company, including the product. Now we have a positive feedback loop because we better understand how our products are working in the field,” says Stefanon.
IMA is already thinking about the future
IMA isn’t stopping there. They have their sights set on incorporating new features and technologies to build on the solutions they’ve created. Specifically, they want to raise the bar with artificial intelligence (AI) by improving on their anomalous and predictive algorithms. By applying analytics and AI to a variety of machines, IMA could disseminate services to more customers on a broader scale. They also plan to leverage augmented reality (AR) in conjunction with AI to deliver insights to frontline workers and create new service tools.
“We’re always focused on making sure our customers can access higher levels of service and increasingly intelligent machines,” says Stefanon. IMA and PTC are excited to continue their decades-long partnership and deliver more value to customer.