Understanding production capabilities is key to staying nimble

The key to success for any business is staying agile and ready for whatever challenges the market presents. But to pivot in a new direction, businesses must first have in place the underlying technology needed to adapt their operations and even create new products. One organization that leveraged state-of-the-art technology to show their agility and help produce a new product at just the right time is Strama-MPS.
Strama-MPS is a German-based solution provider in custom machine and plant engineering, well known as a technological leader in the automotive and automotive supply industries. Founded in 1946 as a one-person engine repair and overhaul company, they now have 1,300 employees at subsidiaries across three continents. Today, Strama-MPS makes the complex machinery needed to produce special automotive parts for OEM customers like BMW and Porsche.
When the competition heated up, Strama-MPS turned to ThingWorx for improved data monitoring and analysis
After 73 years of experience producing machinery for international customers, Strama-MPS began to see the competitive landscape changing, with more competitors adopting IoT technology. Knowing they wanted to remain a leader in their space by embracing the latest tools and provide the best experience for customers, they turned to PTC, the leader in IoT technology.
In March 2020, Strama-MPS chose PTC’s ThingWorx, an end-to-end IIoT platform, to develop an application for connecting customer machines with the goal of improved data analysis, OEE, and service for those customers. “Having done our research, we were confident that ThingWorx could provide the flexibility and ease of use that we needed to optimize machine performance,” says Florian Straßl, Software Engineer. “We want to create a better, more efficient product for our customers, and we knew PTC could help us visualize a direct path there by starting with ThingWorx.”
With plans underway, they went to work developing the new application, not yet aware of how their mission would change in an unexpected way in the months ahead.
Leveraging progress for the greater good
With development in progress, Strama-MPS quickly found themselves—like many other businesses around the world during the spring of 2020—working in the midst of the COVID-19 global pandemic. Despite this new normal, they pressed forward on their IoT application. During development, the executive team received an unusual production request from a business associate to make protective medical masks. Recognizing the opportunity to leverage their progress with ThingWorx and contribute to a critical community need, Strama-MPS agreed. They purchased five mask-making machines, which arrived on site from a local German facility between July and October, around the same time development was wrapping on their ThingWorx application.
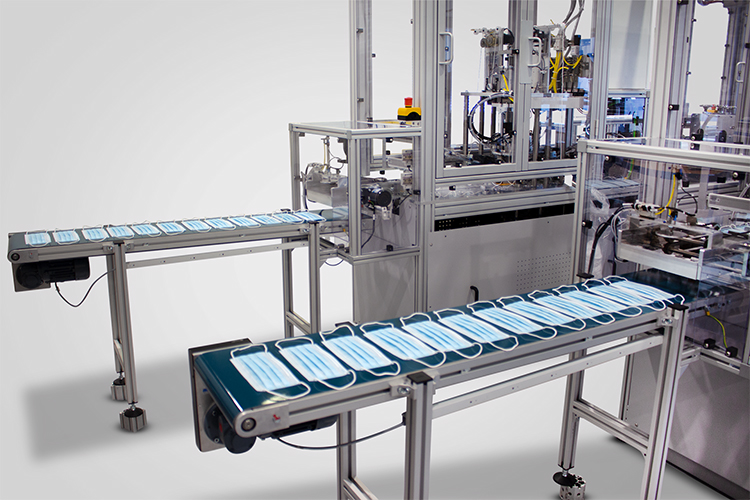
After some initial test runs on the new machines, the team realized that some adjustments would be useful. But in order to refine and optimize the mask making process, they needed more data from the mask machines. Eager to test their new IoT application, they applied ThingWorx technology to test the mask machines for OEE and availability, as well as to compare performance across all five machines. Based on the new data, they were able to identify which of the machines needed adjustments to optimize performance. After making the necessary adjustments, the fifth machine started running at optimal performance alongside the others. It was clear that ThingWorx technology had provided the precise testing abilities and data analysis they needed to ensure their equipment would hit production goals.
Ultimately, the work Strama-MPS had already done with ThingWorx is what enabled the agility needed to go from making special-purpose industrial machinery to delicate medical masks—a very different purpose than their normal business operations—and they were able to turn around the entire process within approximately one month. And as an agile organization, Strama-MPS was able to quickly redirect their people and priorities toward an opportunity to create value, not only for the business but for the community at large.
All told, they produced three different types of masks—two types of surgical masks to be distributed by their business associate, and a third “ProMoMask” designed for community use and distributed by Strama-MPS in addition to regular donations for local hospitals, schools, and non-profits. “What we were able to do was to use the technology we had already developed to scale dynamic capabilities and empower our team to reach an entirely new audience,” says Straßl. “When you see your development transferring from one instance to another very different instance—but it still works just like you intended in your dreams—that’s how you know the technology is really working. To be able to adapt something from test unit to full reproduction over a 30-day period, it’s just very exciting.”
The journey is just beginning
Now that their IoT application is fully developed, Strama-MPS is beginning to put their data analysis capabilities to good use by going to market with their new customer offering. They developed a new app, wherein customers can choose options from pure data analysis to the complete optimization of processes. Specifically, they can identify anomalies, analyze data, view error history, and predict the effects of change, leading to improved throughput and OEE. And because ThingWorx can be flexibly deployed, customers don’t have to worry about data access and control. “By using ThingWorx we can start the application anywhere,” says Straßl. “We can develop a platform for them, but it doesn't matter if the customer wants it locally or globally, so it’s quite convenient and secure.”

Even more helpful to customers is the flexibility around servicing. If they have a service issue, they have the option to simply contact the service department, and engineers can connect into the customer’s machines and see the data using a token to get through the firewall. If a service engineer needs to go on site, that engineer is already equipped with information about the machine’s issue, making for a smooth process for all parties.
With many quantifiable improvements yet to come, it has become obvious that ThingWorx has laid the foundation for future success. As the year moves forward, Strama-MPS continues to refine and perfect their mask-making skills, with plans to add an automated vision inspection feature for enhanced quality control. It’s a sign that they’ve not only accepted a new workload, but also embraced their role as an important part of the community—one that will help others even when it’s not in the blueprints.
Strama-MPS is looking forward to building out their portfolio of new technologies, with plans to explore cloud technology in the near future. Whichever turn Strama-MPS takes next—whether part of their planned journey or unexpected community assist—PTC technologies will be ready to support.
Florian Straßl, Software Engineer