Sometimes seeing is believing, as Texmark can attest. When outdated systems threatened worker and operational efficiencies, they turned to an ecosystem of experienced technology partners to open their eyes to improved ways of working. Learn how advanced technologies like IoT and augmented reality are helping exceed expectations and reduce time to value.
Texmark is a leader in chemical processing and manufacturing
As manufacturers across the highly competitive oil and gas industry can attest, digitally transforming operations can be the difference between surviving and thriving. Texmark Chemicals, Inc. might even say that at the heart of a truly successful digital transformation is the group of people that made it happen.
Texmark is a Texas-based chemical processing and specialty toll-manufacturing leader whose products include DCPD, renewable fuels, mining chemicals, alcohols, and aromatic solvents. Texmark is committed to safely and efficiently meeting customers’ needs and exceeding their expectations with state-of-the-art equipment and highly trained professionals.
Outdated systems and inherent industry risks increase liability costs
Due to the volatile nature of chemical compounds, safety and compliance are of the utmost importance within the chemical manufacturing industry. Meticulous record keeping, secure data storage, and well-maintained and properly functioning equipment are all necessary for safe operations.
While Texmark takes these safety requirements seriously, they had in the past relied mostly on traditional processes and data collection tools to ensure systems remained in working order. For example, to get process performance information while in the field, operators had to radio the control center to request it, rather than use live data for a quicker update. What’s more, walk-throughs were time consuming and labor intensive. They had to check all equipment on fixed schedules, rather than focus on which ones needed attention first. Texmark also had to juggle communication tools while making manual adjustments to the equipment, slowing the process. Finally, data collection was largely paper-based via forms and spreadsheets, creating additional inefficiencies.
Due to steady technological progress and regulatory compliance mandates within the industry, these inefficiencies put Texmark’s mechanical integrity (MI) program at risk for higher operational costs. In fact, their insurance company doubled their deductible from the previous rate. At that point, Texmark knew a change was in order.
They needed modernized equipment and a more systematic approach to collecting and analyzing data so they could improve their MI program ratings, ensuring they maintained the highest levels of safety and regulatory compliance.
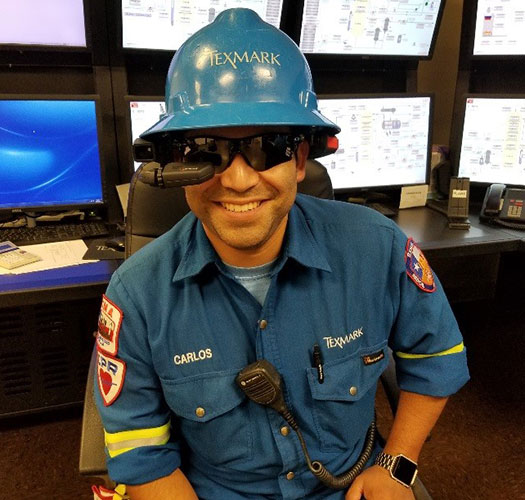
Industrial IoT technology emerges as a must-have
Committed to continuous improvement, Texmark’s leadership analyzed ways to bring more efficiencies to their distributed control system (DCS) and MI program. Texmark consulted with industry colleagues at Hewlett Packard Enterprise, who encouraged them to consider industrial IoT solutions and invited the Texmark team out to their on-site IoT lab.
Unfamiliar with IoT technology but recognizing any change would impact members from across the business, Texmark rented a bus, planned a team bonding trip, and brought employees from engineering, maintenance, sales, operations, senior management, and more.
During the lab visit, the light bulb moment was seeing a smart connected centrifugal pump with sensors that could perform real-time data analysis and predict when the pump would fail. The pump was similar to ones in operation throughout the Texmark production facility, and it made the Texmark team want to know more.
“Everyone wanted an IoT solution at that point because we could all see the value,” says Linda Salinas, VP of Operations at Texmark. “Management saw less time spent taking care of pumps that didn’t require attention, and operators saw less risk to employees,” she continues. “If this is what IoT is, throw a whole bunch in the back of the truck, because we want it.”
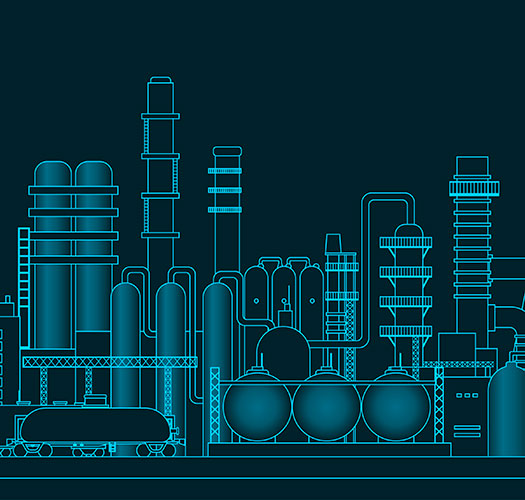
Texmark launches their journey to build a Refinery of the Future, with CB Technologies leading an ecosystem of partners
Soon after the tour at Hewlett Packard Enterprise, Texmark convened a meeting to identify an ecosystem of technology partners. Among others, they recognized the vast potential for a partnership with PTC and CB Technologies (CBT), a premier Domain Expert Integrator with expertise in IT/OT convergence, to create a roadmap for digital transformation.
The CBT team quickly and seamlessly integrated with Texmark, and together they began leveraging ThingWorx, PTC’s end-to-end Industrial IoT platform, and Vuforia Enterprise Augmented Reality (AR) Suite to explore two key use cases that will eventually lay the foundation for digitally transforming operations: Connected Worker and Condition Monitoring and Predictive Maintenance.

Connected Worker
Texmark is using Vuforia Studio—an efficient AR authoring and publishing solution—to begin exploring and developing tailored AR experiences that can be enabled on hands-free devices. These experiences help front-line workers visualize, consume, and communicate important assembly, safety, and repair instructions to others. With these AR capabilities in progress, Texmark is eager to incorporate them into regular operational processes.
Additionally, they are beginning to leverage ThingWorx for real-time data to improve performance insights. ThingWorx data extracted from pumps is fed into digital dashboards tailored to each identified plant persona, enabling access to real-time conditions. In turn, this helps workers make more informed decisions in real time.
Texmark is also currently exploring the addition of handheld smart phones and tablets that will allow workers to view live data on all connected assets.
Condition Monitoring and Predictive Maintenance
Using ThingWorx, they have connected a boiler feedwater pump and a distillation tower’s vacuum pump, providing access to real-time data on asset performance. With a handheld device, personnel will be able to review readings on the condition of a particular asset and determine that the asset is going to fail in a week, day, or hour, and then schedule maintenance around those instances. If a problem arises with a pump sooner, an operator will be notified via a real-time dashboard alert and can then place a work order.
The maintenance person can access the AR experience created with Vuforia Studio on their tablet and follow the directions to locate the pump on a 3-D model of the plant. Once the pump is located, they can view performance attributes in real-time, digitally overlaid onto the physical work environment. Based on the data, and after a physical inspection, they will be able to determine if an adjustment is needed. If it is, then they can correct the issue by following step-by-step instructions, also available in the AR maintenance experience.
With these capabilities proven through real-time demos across the facility, Texmark is eager to implement them into regular operations.
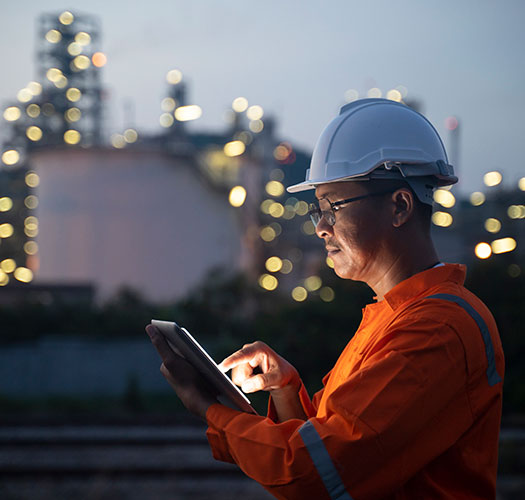
Texmark expects reduced time to value and exceeds compliance expectations
Based on the Connected Worker use case, Texmark is expecting to see up to a 90% reduction in time to file necessary compliance confirmations. Similarly, they’re projecting up to a 75% reduction in time to identify asset malfunctions. Finally, based on the Condition Monitoring and Predictive Maintenance use case, Texmark expects a 50% reduction in planned maintenance costs and has identified the potential to reduce 1,000 hours per year conducting walk-downs and vibration analyses. Clearly, there are many improvements well in the making.
Texmark, CBT, and ecosystem partner Antea Web are continuing to explore and implement additional use cases to facilitate operational improvements—including an important one that has already been achieved: the successful return of their insurance deductible, which was previously doubled, back down to its original amount. To do so, they are taking a digital twin approach and are uploading mechanical integrity asset inspection data, which enables faster decision making, helps maintain regulatory compliance, and makes them more efficient at planning maintenance and expansion activities.
Texmark’s digital transformation has been quite a journey, and they’ve learned important lessons along the way. Salinas urges the importance of getting buy-in from all levels of the organization, not just management. “You’ve got to have every part of your team engaged in every step of the process, including field and floor personnel,” she says. “And you’ve got to listen to them, because they’re the ones who see it in the field every day, and they are going to tell you where to apply the technology to fix certain challenges that will otherwise cost the business a lot of money. Listen, know what’s possible, let them know what’s in the toolbox,” she continues. “If you make their jobs easier, they’re going to do them more efficiently, more safely, and more cost effectively.”
Equally important is having a vision, explains Charlie Stack, Chief Technologist, Operational Technology at CBT. “There’s nothing wrong with thinking over the horizon, because if your thoughts are always over the horizon, then you’re never losing interest on the journey.”
Finally, Texmark believes that getting widespread acceptance of change sometimes just takes one person. “When people are resistant to change, sometimes it just takes one champion, one leader on one team who pushes the technology to his or her group,” says Doug Smith, CEO at Texmark. “Eventually the word will get around and people will say ‘why can’t we get it too?’ It’s the power of people as a combined power of one that can gradually move a company forward.”
With this philosophy leading their work, Texmark is excited to continue their journey toward their Refinery of the Future, knowing that their strong partner ecosystem will support every step of the way.