Ranked among the top 10 European Electronics Manufacturing Services (EMS), LACROIX Electronics, a member of LACROIX group, specializes in electronic subcontracting for the industrial, home automation, automotive, civil avionics and defense, and health sectors. LACROIX Electronics offers global industrial solutions from design to mass production of electronic assemblies and subassemblies.
The Challenge
LACROIX Electronics was looking for ways to gain real-time visibility into the production processes and testing of components, while improving industrial data collection to improve identification of equipment failure and component defects. As part of LACROIX Electronics’ operational excellence strategy, the financial and productivity stakes were high and any solution could not impact production, given that many of their plants handle more than 10 million components every day. The solution also needed to be flexible and scalable across multiple plants with varying levels of automation, connectivity, assets, IT and OT systems.
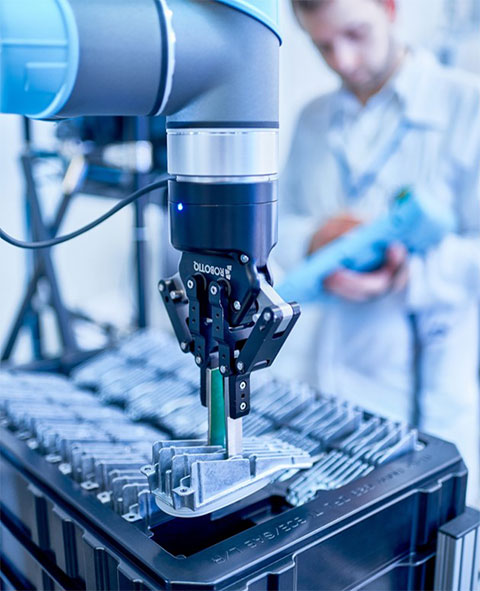
Approach
LACROIX Electronics engaged the advisory services
of KPMG to tender several technical and financial
requirements, five major ones. LACROIX Electronics’
new solution had to be:
- Developed using modern and easily maintained computer languages
- Open and interoperable thereby enabling LACROIX Electronics to remain fully independent in its developments
- Capable of connecting to a highly heterogeneous installed base of machines, both in terms of functionality and duration of use, ages varying from a few months to several years old
- Equipped with functionalities that can easily evolve to Industry 4.0
- Capable of providing clear acquisition and operating costs and easy ROI calculation
Learn More about PTC’s Partnership with KPMG
After consultations with several SCADA and/or MES specialist ISVs, the solution finally selected was ThingWorx from PTC. This choice was then confirmed after completing a feasibility study in collaboration with systems integrator ARDTIC. First deployed on the French site, ThingWorx is currently deployed to LACROIX Electronics’ other plants.
The Solution
PTC’s ThingWorx Industrial IoT platform aggregates data from IT and OT systems including SDM lines, ovens, welding stations or any other machine – to provide accurate, real-time machine status information. In the event of an incident, with this data and visibility, operators can easily analyze and correct the issue, so they can quickly restart production and reduce downtime. This results in scrap reduction, quality improvement, and operational efficiency – helping improve OEE and drive manufacturing excellence. The information from the production lines provided by ThingWorx is displayed in customizable dashboard and accessible on monitors located at the end of the lines, displaying very highly visual indications, thereby facilitating the daily routines and decision-making of the operators and team leaders. In addition, where necessary, employees can also access this information remotely on any type of mobile device. On a site covering an area of 12,000m², this is what mobility is all about! A project this complex can only work because there’s ease of implementation and adoption by all parties involved. With ThingWorx, LACROIX Electronics can rely on an interoperable solution that easily integrates into its existing systems and offering rapid application development and built-in integration capabilities. And thanks to LACROIX Electronics’ change management strategy involving plant operators at a very early stage of the project, they were able to understand the benefits of ThingWorx and adopt it to improve industrial performance under review.
The Next Steps
PTC’s ThingWorx has ensured LACROIX Electronics’ ability to implement a key element of its Smart Industry strategy. The data collected ensures better knowledge of machine status, a complete view of production lines, and earlier detection of anomalies and maintenance requirements. LACROIX Electronics’ original goal was to reduce losses and maximize savings in connection with its Symbiose project to create a new electronic factory of the future in France, and now considers going far beyond data connectivity. For instance, the implementation of predictive maintenance, to approach operational excellence or deliver powerful experiences with Augmented Reality, is under review.
LACROIX Electronics: smart industry, IoT, and digitalization.
Emmanuel Thommerel, VP IT